Cantilever mixed type dry vacuum pump
A dry vacuum pump and hybrid technology, applied in the direction of rotary piston/swing piston pump components, rotary piston pumps, pumps, etc., can solve problems such as unguaranteed, performance degradation of screw pumps, and dead angles in channels, etc., to achieve Reasonable design and compact structure
- Summary
- Abstract
- Description
- Claims
- Application Information
AI Technical Summary
Problems solved by technology
Method used
Image
Examples
Embodiment Construction
[0036] Embodiments of the technical solutions of the present invention will be described in detail below in conjunction with the accompanying drawings. The following examples are only used to illustrate the technical solutions of the present invention more clearly, and therefore are only examples, rather than limiting the protection scope of the present invention.
[0037] It should be noted that, unless otherwise specified, the technical terms or scientific terms used in this application shall have the usual meanings understood by those skilled in the art to which the present invention belongs.
[0038] This embodiment provides a cantilever hybrid dry vacuum pump, such as Figure 1 to Figure 3 As shown, it includes a cantilever shell 1, a cantilever rotor cover 2, a cantilever end cover 3, a non-cantilever body, a gear end cover 6 and a sealed motor connection seat 7 arranged horizontally and connected in sequence. In this embodiment, the non-cantilever The body includes thr...
PUM
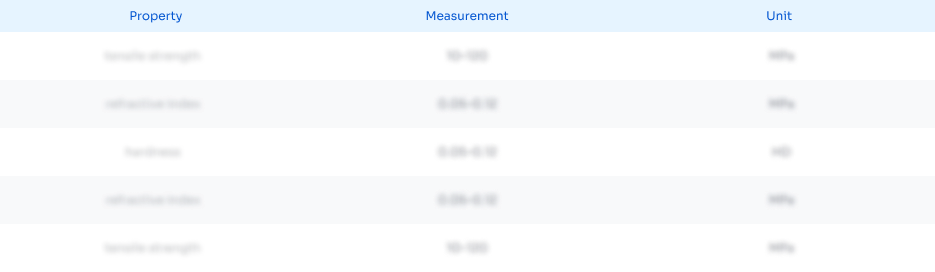
Abstract
Description
Claims
Application Information

- R&D
- Intellectual Property
- Life Sciences
- Materials
- Tech Scout
- Unparalleled Data Quality
- Higher Quality Content
- 60% Fewer Hallucinations
Browse by: Latest US Patents, China's latest patents, Technical Efficacy Thesaurus, Application Domain, Technology Topic, Popular Technical Reports.
© 2025 PatSnap. All rights reserved.Legal|Privacy policy|Modern Slavery Act Transparency Statement|Sitemap|About US| Contact US: help@patsnap.com