Method for fully continuously preparing waterborne polyurethane through prepolymerization-emulsification
A water-based polyurethane, fully continuous technology, applied in the direction of climate sustainability, sustainable manufacturing/processing, chemical industry, etc., can solve problems affecting product quality, destroying raw material ratio, difficult emulsification, etc., to achieve controllable product structure, Increased reactivity and less side effects
- Summary
- Abstract
- Description
- Claims
- Application Information
AI Technical Summary
Problems solved by technology
Method used
Examples
Embodiment 1
[0029] Formula: (parts by weight)
[0030] 80 parts polymer diol: polyethylene carbonate diol (Mn=3000)
[0031] 50 parts Diisocyanate: Isophorone Diisocyanate
[0032] 2 parts small molecule chain extender: 1,3-propanediol
[0033] 5 parts Hydrophilic Chain Extender: Methyldiethanolamine
[0034] 0.055 parts Catalyst: dibutyltin dilaurate
[0035] 300 parts deionized water
[0036] 1.93 parts neutralizer: formic acid
[0037] 2 parts post-chain extender: Ethylenediamine
[0038] Preparation:
[0039] (1) Mix 50 parts of isophorone diisocyanate, 80 parts of polyethylene carbonate diol (Mn=3000), 2 parts of small molecule chain extender (1,3-propanediol), hydrophilic chain extender (A Diethanolamine) 5 parts, catalyst (dibutyltin dilaurate) 0.055 parts, mixed evenly, and then preheated to 100 ° C, continuously injected into the first stage twin-screw reactor, the reaction temperature was controlled at 120 ° C, and the reaction time was 3 minutes;
[0040] (2) After the ...
Embodiment 2
[0047] Formula: (parts by weight)
[0048] 200 parts polymer diol: polyethylene carbonate diol (Mn=2000)
[0049] 100 parts diisocyanate: toluene diisocyanate
[0050] 6 parts small molecule chain extender: 1,4-butanediol
[0051] 15 parts Hydrophilic Chain Extender: Dimethylolpropionic Acid
[0052] 0.15 parts Catalyst: bismuth isooctanoate
[0053] 400 parts deionized water
[0054] 10 parts Neutralizer: Dimethylethanolamine
[0055] 2.5 parts post-chain extender: hydrazine hydrate
[0056] Preparation:
[0057] (1) 100 parts of toluene diisocyanate, 200 parts of polyethylene carbonate diol (Mn=2000), 6 parts of small molecule chain extender (1,4-butanediol), 6 parts of hydrophilic chain extender (dihydroxy 15 parts of methylpropionic acid) and 0.15 parts of catalyst (bismuth isooctanoate) were mixed evenly, then preheated to 120°C, and continuously injected into the first stage twin-screw reactor, the reaction temperature was controlled at 130°C, and the reaction tim...
Embodiment 3
[0065] Formula: (parts by weight)
[0066] 300 parts polymer diol: polyethylene glycol (Mn=2000)
[0067] 180 parts diisocyanate: hexamethylene diisocyanate
[0068] 8 parts small molecule chain extender: ethylene glycol
[0069] 20 parts Hydrophilic chain extender: sodium 1,4-butanediol-2-sulfonate
[0070] 0.22 parts Catalyst: bismuth laurate
[0071] 400 parts deionized water
[0072] 2 parts post-chain extender: p-phenylenediamine
[0073] (1) Mix 180 parts of hexamethylene diisocyanate, 300 parts of polyethylene glycol (Mn=2000), 8 parts of small molecule chain extender (ethylene glycol), hydrophilic chain extender (1,4-butanedi Alcohol-2-sodium sulfonate) 20 parts, catalyst (bismuth laurate) 0.22 parts, mixed evenly, then preheated to 120 ° C, and continuously injected into the first twin-screw reactor, the reaction temperature was controlled at 140 ° C, and the reaction time was 2 minutes;
[0074] (2) After the first stage of reaction is completed, the material e...
PUM
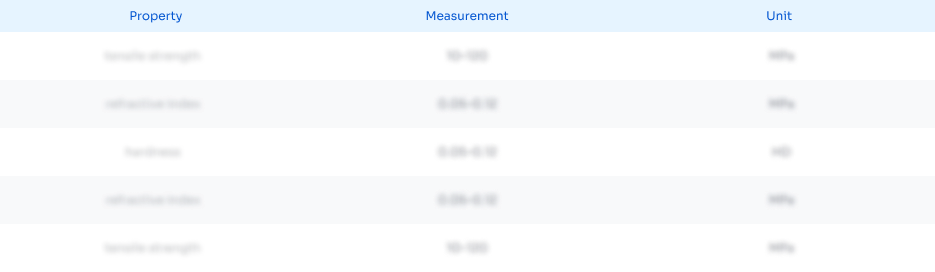
Abstract
Description
Claims
Application Information

- R&D Engineer
- R&D Manager
- IP Professional
- Industry Leading Data Capabilities
- Powerful AI technology
- Patent DNA Extraction
Browse by: Latest US Patents, China's latest patents, Technical Efficacy Thesaurus, Application Domain, Technology Topic, Popular Technical Reports.
© 2024 PatSnap. All rights reserved.Legal|Privacy policy|Modern Slavery Act Transparency Statement|Sitemap|About US| Contact US: help@patsnap.com