Manufacturing method of antenna oscillator and product
A technology of antenna vibrator and manufacturing method, which is applied in the field of composite materials and communication, and can solve problems such as complicated installation, insufficient mature solutions, and heavy material weight
- Summary
- Abstract
- Description
- Claims
- Application Information
AI Technical Summary
Problems solved by technology
Method used
Examples
Embodiment 1
[0030] (1) Metal material having a predetermined structure (the aluminum alloy in this example) is produced;
[0031] (2) The existing process parameters are prepared, and the thermoplastic laser direct molding material is prepared, which is pulverized under low temperature environments, resulting in a thermoplastic laser direct molding material powder (total amount of raw material is 10 kg, according to weight percent, the components are as follows: polycarbonate 41.2 wt%, PBT 45 wt%, LDS additive 4 wt%, kaolin 9 wt%, other additives 0.8 wt%, the polycarbonate in this example uses polycarbonate containing bisphenol A, including two types: polycarbonate At 300 ° C, 1.2 kg of MFR was 8 g / min, the weight average molecular weight was 20 wt%; a polycarbonate was 300 ° C, 1.2 kg of MFR was 18 g / min, and the weight average molecular weight is 19500. The weight percentage of weight is 21.2 wt%. The characteristics of the PBT used in this example are 1.3. In this example, the LDS addi...
Embodiment 2
[0036] (1) Metal material having a predetermined structure (the aluminum alloy in this example) is produced;
[0037] (2) Using the existing process parameters, a thermoplastic laser direct molding material is prepared, and pulverized in a low temperature environment, it is obtained by the thermoplastic laser direct molding material powder (the total amount of raw material is 10 kg, according to the percentage of weight, the components are as follows: LCP62.4WT %, LDS additives 6 wt%, silica grayite 30 wt%, other additives 1.6 wt%, the LDS additive is a basic phosphate in this example);
[0038] (3) Adsorption of a layer of epoxy resin as a film forming material and form a coating (having a thickness of 10 microns); after the powder spraying will use powder spraying to adsorb the laser body to the vibrator body, form laser direct Forming material coating; coating has an average thickness of 300 microns;
[0039] (4) Produce conductive lines on the surface of the vibrator body to o...
PUM
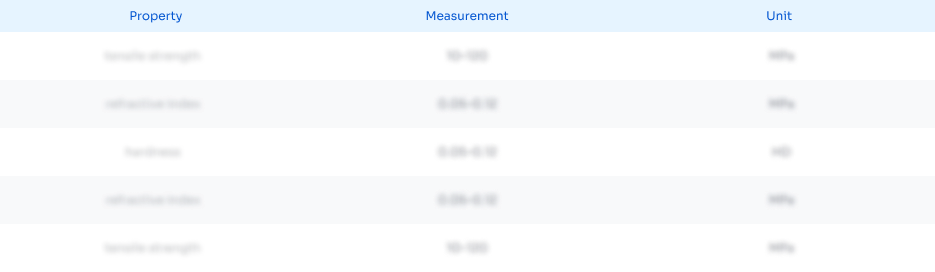
Abstract
Description
Claims
Application Information

- R&D
- Intellectual Property
- Life Sciences
- Materials
- Tech Scout
- Unparalleled Data Quality
- Higher Quality Content
- 60% Fewer Hallucinations
Browse by: Latest US Patents, China's latest patents, Technical Efficacy Thesaurus, Application Domain, Technology Topic, Popular Technical Reports.
© 2025 PatSnap. All rights reserved.Legal|Privacy policy|Modern Slavery Act Transparency Statement|Sitemap|About US| Contact US: help@patsnap.com