A method for reducing catalyst carbon deposition in hfc-23 resource utilization
A technology of HFC-23 and catalyst is applied in the field of HFC-23 resource utilization, which can solve the problems of reduced product selectivity, and achieve the effects of improving stability, inhibiting carbon deposition, and improving stability and life.
- Summary
- Abstract
- Description
- Claims
- Application Information
AI Technical Summary
Problems solved by technology
Method used
Image
Examples
Embodiment 1
[0034] Preparation of catalyst: Pretreatment of chromium trioxide catalyst (main catalyst), the pretreatment process includes: 1) 10% hydrogen fluoride and 90% nitrogen mixed atmosphere, 250 ℃ fluorination treatment for 2 hours; 2) hydrogen fluoride atmosphere, Treat at 300°C for 5 hours; 3) Purge with nitrogen to cool down. Pour the fluorinated pretreated catalyst into n-hexane, stir and disperse evenly, add Ru nano-colloid dispersion drop by drop, control the mass content of Ru loading to 0.1%, continue stirring for 4 hours and then let stand, the upper layer of the solution becomes transparent After clarification, it was transferred to a rotary evaporator, rotary evaporated to dryness at 80 °C, dried in an oven at 110 °C overnight, and calcined in a muffle furnace at 400 °C for 6 hours to obtain a shaped catalyst, which was recorded as catalyst 1.
[0035] HFC-23 resource utilization: pass trifluoromethane, chloroform and hydrogen at 1:1.5:0.2 (molar ratio) into the reactor e...
Embodiment 2
[0037] Preparation of catalyst: Pretreatment of chromium trioxide catalyst (main catalyst), the pretreatment process includes: 1) 10% hydrogen fluoride and 90% nitrogen mixed atmosphere, 250 ℃ fluorination treatment for 2 hours; 2) hydrogen fluoride atmosphere, Treat at 300°C for 5 hours; 3) Purge with nitrogen to cool down. Pour the fluorinated pretreated catalyst into n-hexane, stir and disperse evenly, add Pt nano-colloid dispersion drop by drop, control the loading of Pt at 0.1 wt%, keep stirring continuously for 4 hours, and the upper layer of the solution becomes transparent and clear Then transferred to a rotary evaporator, rotary evaporated to dryness at 80°C, dried overnight at 110°C in an oven, and calcined at 400°C for 6 h in a muffle furnace to obtain a shaped catalyst, denoted as catalyst 2.
[0038] HFC-23 resource utilization: pass trifluoromethane, chloroform and hydrogen at 1:1.5:0.2 (molar ratio) into the reactor equipped with 50ml of catalyst 2, the reaction...
Embodiment 3
[0040] Preparation of catalyst: Pretreatment of chromium trioxide catalyst (main catalyst), the pretreatment process includes: 1) 10% hydrogen fluoride and 90% nitrogen mixed atmosphere, 250 ℃ fluorination treatment for 2 hours; 2) hydrogen fluoride atmosphere, Treat at 300°C for 5 hours; 3) Purge with nitrogen to cool down. Pour the fluorinated pretreated catalyst into n-hexane, stir and disperse evenly, add Pd nano-colloid dispersion drop by drop, control the mass loading of Pd at 0.1%, keep stirring continuously for 4 hours, and the upper layer of the solution becomes transparent and clear Then transferred to a rotary evaporator, rotary evaporated to dryness at 80 °C, dried overnight at 110 °C in an oven, and calcined in a muffle furnace at 400 °C for 6 h to obtain a shaped catalyst, which was recorded as catalyst 3.
[0041] HFC-23 resource utilization: pass trifluoromethane, chloroform and hydrogen into a reactor equipped with 50ml of catalyst 3 at 1:1.5:0.2 (molar ratio)...
PUM
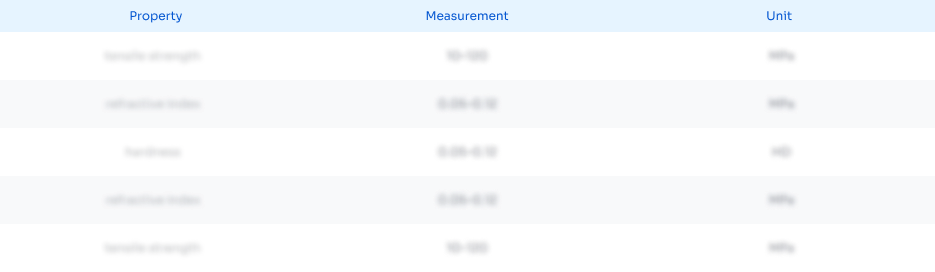
Abstract
Description
Claims
Application Information

- Generate Ideas
- Intellectual Property
- Life Sciences
- Materials
- Tech Scout
- Unparalleled Data Quality
- Higher Quality Content
- 60% Fewer Hallucinations
Browse by: Latest US Patents, China's latest patents, Technical Efficacy Thesaurus, Application Domain, Technology Topic, Popular Technical Reports.
© 2025 PatSnap. All rights reserved.Legal|Privacy policy|Modern Slavery Act Transparency Statement|Sitemap|About US| Contact US: help@patsnap.com