Production method of densified bamboo board
A production method and compact technology, applied in wood processing, wood processing appliances, wood processing details, etc., can solve the problems that restrict the large-scale use of bamboo, the natural structure of the material is easily damaged, and the hemicellulose is easy to absorb moisture, etc., and achieves a green production process. Environmentally friendly, conducive to rebound setting, uniform material effect
- Summary
- Abstract
- Description
- Claims
- Application Information
AI Technical Summary
Problems solved by technology
Method used
Image
Examples
Embodiment 1
[0028] The production method of the compacted bamboo plate in the present embodiment comprises following method:
[0029] Bamboo chip production: Cut the bamboo into sections and slice them, classify them according to the diameter of the small head, and cut them into two halves along the diameter direction, then polish the protruding part of the bamboo partition on the green surface, mill the yellow surface to determine the thickness, remove the inner nodes and 2-3mm bamboo yellow is made into bamboo slices;
[0030] Pretreatment: put the bamboo slices into the iron frame and immerse them in the pool for 1-2 hours. After the surface is dried, push them into the steam treatment tank, and keep them for 7-10 minutes at a pressure of 1.2-1.5MPa and a temperature of 190-200°C. The rapid softening of the bamboo slices can be realized; the bamboo slices in the steam treatment tank are immediately flattened longitudinally after the pressure is released.
[0031] Longitudinal flatteni...
Embodiment 2
[0043] In a specific example of the present embodiment, the method for making the compacted bamboo board is specifically:
[0044]Select fresh moso bamboo stalks straight to the bamboo section, cut off the root and middle part with a large wall thickness difference to 1.26-1.30m, and cut off the tip with a small wall thickness difference to 2.48-2.50m. The above-mentioned bamboo sections are divided into two types according to the diameter of the small head, 10-13cm and 13-16cm. The bamboo sections with a diameter of 10-13cm are sawed into two half-arc lengths of 15.5-16cm by a bamboo sawing machine with a fixed width. The bamboo section with a diameter of 13-16 cm is sawed and cut into two half-arc lengths of 20.4-21 cm, and the protruding part of the bamboo partition on the green side is polished, and the yellow side is milled with a fixed thickness to remove the inner nodes and 2-3 mm of bamboo yellow.
[0045] Put the bamboo slices into the iron frame and immerse them in t...
PUM
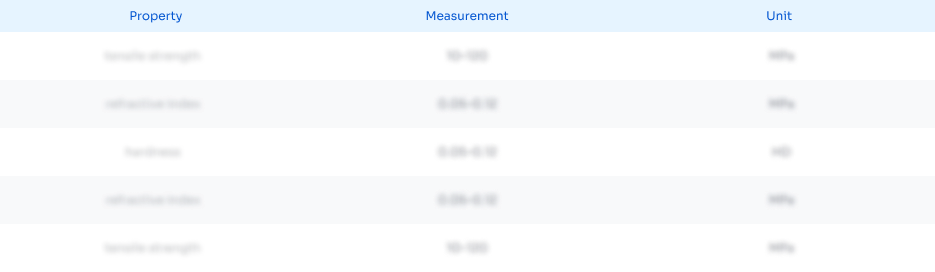
Abstract
Description
Claims
Application Information

- R&D
- Intellectual Property
- Life Sciences
- Materials
- Tech Scout
- Unparalleled Data Quality
- Higher Quality Content
- 60% Fewer Hallucinations
Browse by: Latest US Patents, China's latest patents, Technical Efficacy Thesaurus, Application Domain, Technology Topic, Popular Technical Reports.
© 2025 PatSnap. All rights reserved.Legal|Privacy policy|Modern Slavery Act Transparency Statement|Sitemap|About US| Contact US: help@patsnap.com