Anti-emulsification liquid distribution sleeve and anti-emulsification centrifugal extractor
A centrifugal extractor and anti-emulsification technology, applied in liquid solution solvent extraction, solvent extraction, separation methods, etc., can solve the problems of low mass transfer efficiency, single mixing method, high stagnation rate of ring gap, etc., to improve mass transfer efficiency , reduce stagnation rate, uniform particle size effect
- Summary
- Abstract
- Description
- Claims
- Application Information
AI Technical Summary
Problems solved by technology
Method used
Image
Examples
Embodiment 1
[0050] Such as figure 1 and figure 2 As shown, this embodiment provides a centrifugal extractor in the preparation process of liquid energetic plasticizer nitroazide compound, in which the liquid distribution sleeve of the above design is used.
[0051] Motor 1 is an explosion-proof three-phase asynchronous motor.
[0052] The design of bottom flange 24 adopts 8 vortex vanes as guide vanes, and the distance from the mixed liquid suction inlet of the rotating drum is 5mm.
[0053] In the rotating assembly, diversion holes are provided every 35 mm on the upper part of the outer wall 301 of the drum as the heavy phase outlet 9 and the light phase outlet 10; the interval between the heavy phase weir plate 8 and the light phase weir plate is 20 mm.
[0054] The anti-emulsion cloth liquid sleeve 13 is fixed on the bottom flange 24 by welding.
[0055] The inner diameter of the anti-emulsification liquid distribution sleeve 13 is 1 / 3 of the ring-to-ring ratio difference between t...
Embodiment 2
[0062] This embodiment provides a design of an anti-emulsification device for a centrifugal extractor in the aluminum ammonium sulfate solution for iron removal in the alumina preparation process, including a preferred centrifugal extractor and an annular liquid distribution device on the inner wall of the shell with an anti-emulsification function design plate. Compared with the centrifugal extractor that embodiment 1 provides, the difference is:
[0063] The motor 1 in the transmission part is a non-explosion-proof asynchronous three-phase motor, and the bottom flange 24 is designed to use 6 flat blades as guide vanes, and the distance between it and the mixed liquid suction inlet of the drum is 20 mm.
[0064] The anti-emulsification device is used in the process of extracting alumina from fly ash. Considering the cost of extraction agent dissolution loss and stripping performance effect, two or three of aluminum ammonium sulfate solution, phosphate esters and amine compoun...
Embodiment 3
[0070] This embodiment provides a design of an anti-emulsification device for a centrifugal extractor for the treatment of high-concentration phenol-containing wastewater, including a combined design of a preferred centrifugal extractor and a liquid distribution sleeve 13 with an anti-emulsification function + a liquid distribution structure. Compared with the centrifugal extractor that embodiment 1 provides, the difference is:
[0071] The motor 1 in the transmission part is a non-explosion-proof asynchronous motor, and the bottom flange 24 is designed to use 6 vortex blades as guide blades, and the distance between it and the mixed liquid suction inlet of the drum is 10 mm.
[0072] Considering the microemulsion extractant in the treatment process of high-concentration phenol-containing wastewater, it is often selected from a mixture of tributyl phosphate, medium oil and amine compounds or a trioctylamine solution or a complex extractant plus a mixture of multiple modifiers. ...
PUM
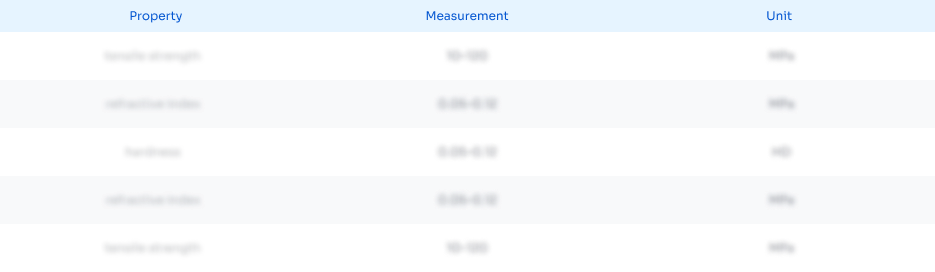
Abstract
Description
Claims
Application Information

- R&D
- Intellectual Property
- Life Sciences
- Materials
- Tech Scout
- Unparalleled Data Quality
- Higher Quality Content
- 60% Fewer Hallucinations
Browse by: Latest US Patents, China's latest patents, Technical Efficacy Thesaurus, Application Domain, Technology Topic, Popular Technical Reports.
© 2025 PatSnap. All rights reserved.Legal|Privacy policy|Modern Slavery Act Transparency Statement|Sitemap|About US| Contact US: help@patsnap.com