Preparation and application of phosphorus-doped graphite carbon nitride/ferroferric oxide composite material
A technology of graphitic carbon nitride and iron tetroxide, which is applied in chemical/physical processes, oxidized water/sewage treatment, special compound water treatment, etc. low rate issues
- Summary
- Abstract
- Description
- Claims
- Application Information
AI Technical Summary
Problems solved by technology
Method used
Image
Examples
Embodiment 1
[0028] (1) Preparation of CNP: Grind urea (10g, 0.17mol) and dipotassium hydrogen phosphate (0.87g, 5mmol) thoroughly and mix them in a crucible with a lid, heat in a muffle furnace at a heating rate of 2.3°C / min Calcined at 500°C for 2~5h, cooled to room temperature, dissolved in distilled water to form a 1g / L solution, ultrasonicated intermittently at 20000~25000 Hz (interval 1~2h, total ultrasonic 3 h), centrifuged, Washing and drying afforded a pale yellow solid labeled CNP.
[0029] (2) CNP / Fe 3 o 4 Preparation of composite materials: 1 g of CNP and 0.027 g of FeCl 3 •6H 2 O was dissolved in 64 ml of ethylene glycol solution to form a light yellow solution, then 3 ml of hydrazine hydrate was added and stirred for 30 min to form a brownish yellow suspension, and the suspension was transferred to a 100 ml polytetrafluoroethylene-lined stainless steel reactor, React at 200 °C for 10 h, centrifuge, wash with deionized water and ethanol, and dry in a vacuum oven at 70 °C f...
Embodiment 2
[0032] (1) Preparation of CNP: Grind urea (10 g, 0.17 mol) and dipotassium hydrogen phosphate (0.87 g, 5 mmol) thoroughly and mix them in a crucible with a lid, and heat up at a rate of 2.3 °C / min in a muffle furnace Heating to 500°C, calcining for 2~5h, cooling to room temperature, adding it into distilled water and dissolving it to form a 1 g / L solution, ultrasonication at 20000~25000 Hz (interval time 1~2h, total ultrasonication 3 h), Centrifugation, washing, and drying afforded a pale yellow solid labeled CNP.
[0033] (2) CNP / Fe 3 o 4 Preparation of composite materials: 1 g of CNP and 0.054 g of FeCl 3 •6H 2 O was dissolved in 64 ml ethylene glycol solution to form a light yellow solution, then added 6 ml hydrazine hydrate and stirred for 30 min to form a brownish yellow suspension, and the suspension was transferred to a 100 ml polytetrafluoroethylene-lined stainless steel reactor, React at 200 °C for 10 h, centrifuge, wash with deionized water and ethanol, and dry i...
Embodiment 3
[0036] (1) Preparation of CNP: Grind urea (10 g, 0.17 mol) and dipotassium hydrogen phosphate (0.87 g, 5 mmol) thoroughly and mix them in a crucible with a lid, and heat up at a rate of 2.3 °C / min in a muffle furnace Heating to 500°C, calcining for 2~5h, cooling to room temperature, dissolving it in distilled water to form a 1 g / L solution, ultrasonication at 20000~25000 Hz (interval 1~2h, total ultrasonication 3 h), Centrifugation, washing, and drying afforded a pale yellow solid labeled CNP.
[0037] (2) CNP / Fe 3 o 4 Preparation of composite materials: 1 g of CNP and 0.108 g of FeCl 3 •6H 2 O was dissolved in 64 ml of ethylene glycol solution to form a light yellow solution, then 12 ml of hydrazine hydrate was added and stirred for 30 min to form a brownish yellow suspension, and the suspension was transferred to a 100 ml polytetrafluoroethylene-lined stainless steel reaction kettle, in React at 200 °C for 10 h, centrifuge, wash with deionized water and ethanol, and dry ...
PUM
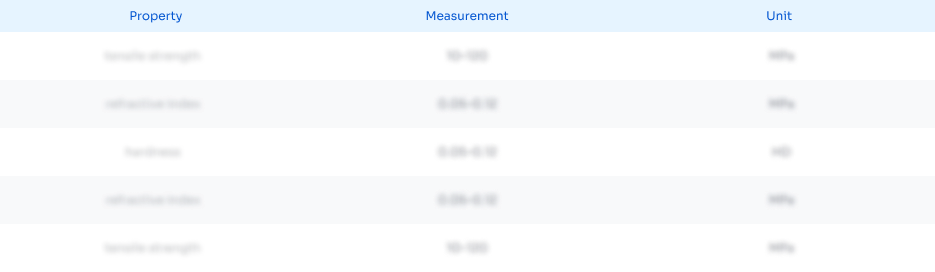
Abstract
Description
Claims
Application Information

- R&D
- Intellectual Property
- Life Sciences
- Materials
- Tech Scout
- Unparalleled Data Quality
- Higher Quality Content
- 60% Fewer Hallucinations
Browse by: Latest US Patents, China's latest patents, Technical Efficacy Thesaurus, Application Domain, Technology Topic, Popular Technical Reports.
© 2025 PatSnap. All rights reserved.Legal|Privacy policy|Modern Slavery Act Transparency Statement|Sitemap|About US| Contact US: help@patsnap.com