Acrylate emulsion and application thereof in aluminum powder paint
An acrylate and emulsion technology, used in coatings, anti-corrosion coatings, etc., can solve the problems of long-term outdoor use, inferior hardness, and high price and cost
- Summary
- Abstract
- Description
- Claims
- Application Information
AI Technical Summary
Problems solved by technology
Method used
Image
Examples
Embodiment 1
[0035] Primer: 20 parts of deionized water, 0.2 parts of nonionic emulsifier, 0.5 part of anionic emulsifier; stir to dissolve;
[0036] Nuclear monomer mixture: 0.5 parts of phosphate functional monomer, 1.5 parts of butyl acrylate, 5 parts of methyl methacrylate, 2 parts of styrene, 2 parts of isooctyl acrylate, 0.2 parts of acrylic acid, hydroxyethyl methacrylate 2 parts of ester;
[0037] Primary initiator aqueous solution: 1 part of deionized water, 0.03 part of APS, dissolved;
[0038] Drop initiator aqueous solution: 5 parts of deionized water, 0.07 parts of APS, dissolve;
[0039] Shell monomer mixture: 8 parts of styrene, 1 part of butyl acrylate, 1 part of isooctyl acrylate, 2 parts of methyl methacrylate, 1 part of hydroxyethyl methacrylate;
[0040] Shell initiator aqueous solution: 1 part of deionized water, 0.05 part of tert-butyl hydroperoxide, dissolved; 1 part of deionized water, 0.05 part of sodium sulfite, dissolved;
[0041] Tert-butyl hydroperoxide solu...
Embodiment 2
[0053] Primer: 40 parts of deionized water, 0.4 parts of nonionic emulsifier, 0.9 part of anionic emulsifier; stir to dissolve;
[0054] Nuclear monomer mixture: 2 parts of phosphate functional monomer, 3 parts of butyl acrylate, 10 parts of methyl methacrylate, 5 parts of styrene, 5 parts of isooctyl acrylate, 0.6 part of acrylic acid, hydroxyethyl methacrylate 8 parts of ester;
[0055] Primary initiator aqueous solution: 2 parts of deionized water, 0.1 part of APS, dissolved;
[0056] Drop initiator aqueous solution: 10 parts of deionized water, 0.15 parts of APS, dissolve;
[0057] Shell monomer mixture: 15 parts of styrene, 4 parts of butyl acrylate, 4 parts of isooctyl acrylate, 8 parts of methyl methacrylate, 4 parts of hydroxyethyl methacrylate;
[0058] Shell initiator aqueous solution: 2 parts of deionized water, 0.2 parts of tert-butyl hydroperoxide, dissolved; 2 parts of deionized water, 0.2 parts of sodium sulfite, dissolved;
[0059] Tert-butyl hydroperoxide s...
Embodiment 3
[0071] Primer: 39 parts of deionized water, 0.28 parts of nonionic emulsifier, 0.75 part of anionic emulsifier; stir to dissolve;
[0072] Nuclear monomer mixture: 0.93 parts of phosphate functional monomer, 2.3 parts of butyl acrylate, 7.5 parts of methyl methacrylate, 3.5 parts of styrene, 3.5 parts of isooctyl acrylate, 0.41 parts of acrylic acid, hydroxyethyl methacrylate 4.66 parts of ester;
[0073] Primary initiator aqueous solution: 1.12 parts of deionized water, 0.07 parts of APS, dissolved;
[0074] Drop initiator aqueous solution: 7.8 parts of deionized water, 0.12 parts of APS, dissolve;
[0075] Shell monomer mixture: 9.8 parts of styrene, 1.4 parts of butyl acrylate, 2 parts of isooctyl acrylate, 4.31 parts of methyl methacrylate, 1.86 parts of hydroxyethyl methacrylate;
[0076] Shell initiator aqueous solution: 2.8 parts of deionized water, 0.12 parts of tert-butyl hydroperoxide, dissolved; 2.8 parts of deionized water, 0.09 parts of sodium sulfite, dissolved...
PUM
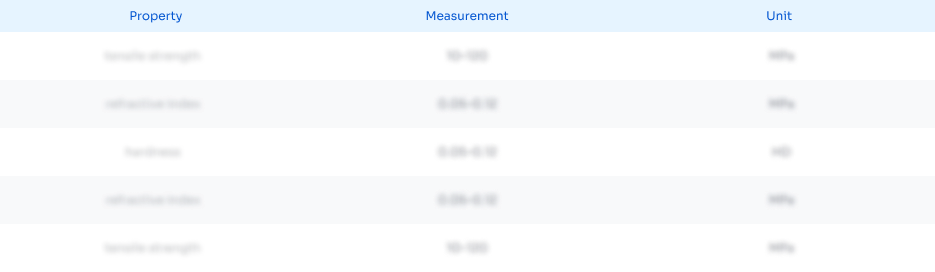
Abstract
Description
Claims
Application Information

- R&D Engineer
- R&D Manager
- IP Professional
- Industry Leading Data Capabilities
- Powerful AI technology
- Patent DNA Extraction
Browse by: Latest US Patents, China's latest patents, Technical Efficacy Thesaurus, Application Domain, Technology Topic, Popular Technical Reports.
© 2024 PatSnap. All rights reserved.Legal|Privacy policy|Modern Slavery Act Transparency Statement|Sitemap|About US| Contact US: help@patsnap.com