Preparation process of copper-based powder contact and relay formed by prepared contact
A copper-based powder, preparation process technology, applied in the direction of relays, electromagnetic relays, electromagnetic relay details, etc., can solve problems such as billet cracks, no cooling steps, etc.
- Summary
- Abstract
- Description
- Claims
- Application Information
AI Technical Summary
Problems solved by technology
Method used
Image
Examples
Embodiment 1
[0034] Such as figure 1 As shown, the preparation process of copper-based powder contacts includes the following steps: S1. Primary powder mixing: raw material copper, raw material bismuth, raw material Al2O3, raw material boron carbide, raw material ditungsten pentaboride, raw material cerium, raw material The lanthanum and raw graphite are finely ground with a high-energy ball mill, and the mixed powder I is obtained after ball milling; S2. Filtration and drying: the mixed powder I is filtered with a filter device to obtain the filtered mixed powder II, and the mixed powder II is Drying under vacuum conditions; S3. One-time pressing: Press the mixed powder II on a hydraulic press with a pressure of 320MPa to form a billet. After the pressing pressure reaches 320MPa, keep the pressure for 2 minutes; S4. Sintering in the atmosphere furnace at 800°C; S5. Cooling: Fill the furnace with a rare gas at room temperature (25°C) for 35 minutes after the primary sintering, and then cha...
Embodiment 2
[0041] The difference between this embodiment and Example 1 is: in the step S1 of this embodiment, the ingredients are different when the raw materials are batched according to the weight components. 1.3 parts of aluminum oxide, 2 parts of raw material boron carbide, 0.9 parts of raw material ditungsten pentaboride, 0.1 part of raw material cerium, 0.07 part of raw material lanthanum, 3 parts of raw material graphite, and 88 parts of raw material copper. In this embodiment, the primary sintering temperature in step S4 is 900° C., the duration of the initial injection of rare gas at room temperature in step S5 is 40 min, and the secondary sintering temperature in step S7 is 500° C. In the same manner as in Example 1, the comparative detection of the crack rate of the billet was carried out. The crack rate of the billet in this embodiment was less than 4.2%. Obviously, this embodiment can significantly reduce the probability of cracks in the billet after secondary pressing.
Embodiment 3
[0043] The difference between this embodiment and Example 1 is that in step S1 of this embodiment, the ingredients are different when the raw materials are batched according to the weight components. 0.5 parts of aluminum oxide, 0.5 parts of boron carbide as a raw material, 1.5 parts of ditungsten pentaboride as a raw material, 0.05 parts of cerium as a raw material, 0.1 part of lanthanum as a raw material, 2 parts of graphite as a raw material, and 96 parts of copper as a raw material. In this embodiment, the primary sintering temperature in step S4 is 1000° C., the duration of the initial injection of rare gas at room temperature in step S5 is 30 minutes, and the secondary sintering temperature in step S7 is 550° C. Using the same method as in Example 1 to carry out comparative detection of the crack rate of the billet, the crack rate of the billet in this embodiment is less than 4.4%. Obviously, this embodiment can significantly reduce the probability of cracks in the billet...
PUM
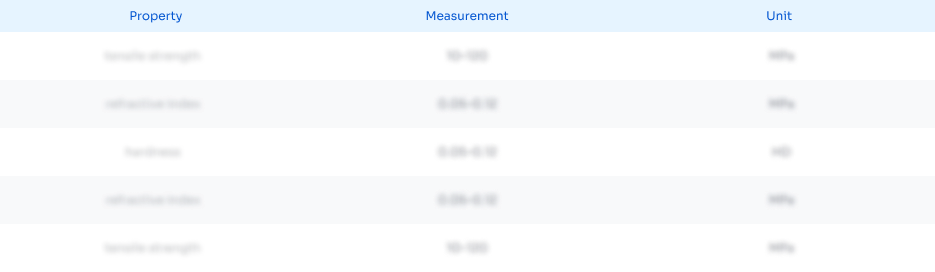
Abstract
Description
Claims
Application Information

- R&D Engineer
- R&D Manager
- IP Professional
- Industry Leading Data Capabilities
- Powerful AI technology
- Patent DNA Extraction
Browse by: Latest US Patents, China's latest patents, Technical Efficacy Thesaurus, Application Domain, Technology Topic, Popular Technical Reports.
© 2024 PatSnap. All rights reserved.Legal|Privacy policy|Modern Slavery Act Transparency Statement|Sitemap|About US| Contact US: help@patsnap.com