Wet separation technology for waste lithium batteries and application thereof
A waste lithium battery, sorting technology, applied in the direction of battery recycling, solid separation, recycling technology, etc., can solve the problems of resource waste, deterioration, unusable, etc., and achieve the effect of low cost
- Summary
- Abstract
- Description
- Claims
- Application Information
AI Technical Summary
Problems solved by technology
Method used
Image
Examples
Embodiment 1
[0042] A wet sorting process for waste lithium batteries, comprising the following steps:
[0043] (1) Perform a stage of wet ball milling under the condition that the ball milling concentration is 60% and the steel ball filling rate is 40% for 1 ton of waste and old ternary square shell lithium battery sorting raw materials to obtain a ball milling product;
[0044] (2) Put the ball mill product into vibrating sieves with mesh sizes of 2mm and 0.15mm respectively for sieving to obtain coarse-grained grades (coarse-grained grade products are returned to the first stage of ball mill feeding), medium-grained grades and fine-grained grades Grade three screened materials;
[0045] (3) The sieved material of the medium particle size is added with water to adjust the concentration to 50%, and the passing condition is that the steel ball filling rate is 45%, and the sieve size is the second stage wet ball milling-sieving of 0.15mm, and the obtained 0.15 Add appropriate amount of wat...
Embodiment 2
[0051] A waste lithium battery wet separation process, comprising the following steps:
[0052] (1) 1 ton of waste lithium cobaltate soft-pack battery sorting raw materials is subjected to a stage of wet ball milling under the conditions that the ball milling concentration is 55% and the steel ball filling rate is 35%, to obtain a ball milling product;
[0053] (2) Put the ball mill product into vibrating sieves with mesh sizes of 2mm and 0.15mm respectively for sieving to obtain coarse-grained grades (coarse-grained grade products are returned to the first stage of ball mill feeding), medium-grained grades and fine-grained grades Grade three screened materials;
[0054] (3) Add appropriate amount of water to the medium-sized product to adjust the concentration to 52%, and pass the second-stage wet ball milling-sieving with a steel ball filling rate of 40% and a sieve size of 0.15mm to obtain a 0.15-2mm The material is added with an appropriate amount of water to adjust the c...
PUM
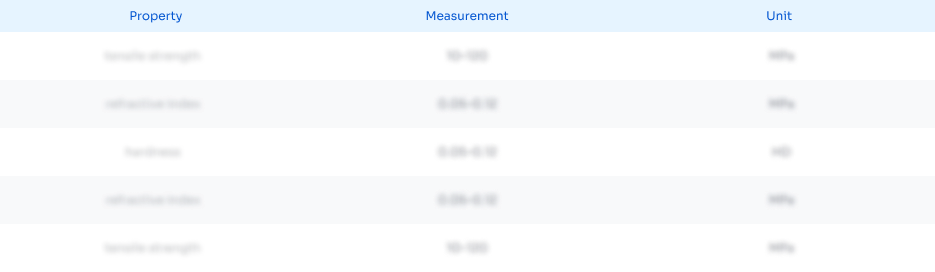
Abstract
Description
Claims
Application Information

- R&D Engineer
- R&D Manager
- IP Professional
- Industry Leading Data Capabilities
- Powerful AI technology
- Patent DNA Extraction
Browse by: Latest US Patents, China's latest patents, Technical Efficacy Thesaurus, Application Domain, Technology Topic, Popular Technical Reports.
© 2024 PatSnap. All rights reserved.Legal|Privacy policy|Modern Slavery Act Transparency Statement|Sitemap|About US| Contact US: help@patsnap.com