Current-assisted SPF/DB integrated forming process
A forming process and current technology, applied in the field of current-assisted SPF/DB integrated forming process, can solve problems such as large total current requirements
- Summary
- Abstract
- Description
- Claims
- Application Information
AI Technical Summary
Problems solved by technology
Method used
Image
Examples
Embodiment 1
[0061] Such as Figure 1-9 As shown, a current-assisted SPF / DB integrated forming mold, the mold includes an insulating mold body 1, and the insulating mold body 1 is provided with a cavity 3 and an assembly hole 2, and the assembly hole 2 is set through the cavity 3 , the assembly hole 2 is equipped with a vertical electrode 4, and the vertical electrode 4 is assembled in the assembly hole 2 and divides the cavity 3 into at least one cavity 5 for sheet material 6 molding (such as Figure 9 As shown, after the vertical electrode 4 is inserted into the assembly hole 2, the inclined surface 41 at the bottom of the vertical electrode 4 ("inclined surface" refers to the outer peripheral surface of the part where the vertical electrode 4 is located in the concave cavity range and the bottom surface of the plate in the present invention) The shape does not constitute a limitation, and is replaced by "inclined surface" in this embodiment only for the convenience of description; in ac...
Embodiment 2
[0066] On the basis of embodiment 1, the part (the inclined surface 41 at the bottom of the vertical electrode) constituting the boundary of the mold cavity 3 on the vertical electrode 4 is an insulating surface, and the insulating surface is coated with an insulating material ( It can be made of high-temperature-resistant insulating materials such as insulating varnish, which are easy to paint, have small thickness and easy control of uniformity, etc.). By coating the insulating material on the inclined surface 41 at the bottom of the vertical electrode constituting the cavity 3, the current when the vertical electrode is energized can be effectively concentrated on the area covered by the bottom surface 42 of the vertical electrode, thereby realizing the diffusion connection of the current in the plate Concentration of regions speeds up the process of diffusion connection of regions to be diffused and connected. Wherein, the material of the insulating mold main body 1 can be...
Embodiment 3
[0068] On the basis of Embodiment 2, the side on the vertical electrode 4 that is used to bond with the plate 6 and electrically heat the area to be diffused and connected to the plate 6 is a heating surface (bottom surface 42 of the vertical electrode in the figure), and the insulating surface is provided with 2 and set on both sides of the heating surface. By respectively setting insulating surfaces (inclined surfaces 41 at the bottom of the vertical electrodes) on both sides of the bottom surface 42 of the vertical electrodes, after the vertical electrodes 4 are assembled in the assembly holes 2, the inclined surfaces 41 on both sides can cooperate with the cavity 3, as The boundary of the cavity 5 used for sheet forming is further applicable to the processing of sheets that need to form multiple hollow structures, improving the efficiency of sheet processing.
PUM
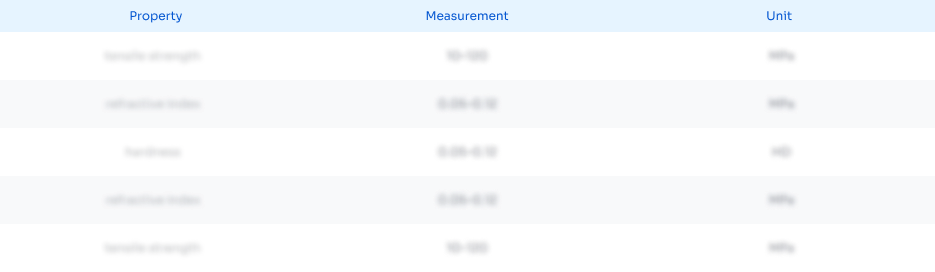
Abstract
Description
Claims
Application Information

- R&D
- Intellectual Property
- Life Sciences
- Materials
- Tech Scout
- Unparalleled Data Quality
- Higher Quality Content
- 60% Fewer Hallucinations
Browse by: Latest US Patents, China's latest patents, Technical Efficacy Thesaurus, Application Domain, Technology Topic, Popular Technical Reports.
© 2025 PatSnap. All rights reserved.Legal|Privacy policy|Modern Slavery Act Transparency Statement|Sitemap|About US| Contact US: help@patsnap.com