A kind of wet process polyurethane resin and its preparation method and application
A wet-process polyurethane and resin technology, which is applied in the field of wet-process polyurethane resin and its preparation, wet-process polyurethane resin for glove protection and its preparation, can solve the problem of low VOC content, resilience of gloves, and poor wear resistance and scratch resistance. The resilience needs to be further improved to achieve the effects of good resilience, good wear resistance and excellent mold release.
- Summary
- Abstract
- Description
- Claims
- Application Information
AI Technical Summary
Problems solved by technology
Method used
Image
Examples
Embodiment 1
[0061] In this embodiment, a wet-process polyurethane resin is provided. The wet-process polyurethane resin includes three components: A, B, and C. By weight percentage, the preparation raw materials of the A component include the following components:
[0062]
[0063] By weight percentage, the preparation raw materials of the B component include the following components:
[0064]
[0065] The C component is composed of cellulose acetate butyrate and SAN resin in a weight ratio of 1:2.
[0066] Wherein, the number-average molecular weight of polyethylene oxide diol is 2000g / mol, the number-average molecular weight of polyethylene adipate diol is 4000g / mol, and the number-average molecular weight of polycaprolactone diol is 2000g / mol, The number average molecular weight of the phthalic anhydride polyester diol is 2000 g / mol; the weight ratio of the A component and the B component is 1:6; the C component accounts for 3% of the total weight of the A component and the B com...
Embodiment 2
[0072] In this embodiment, a wet-process polyurethane resin is provided. The wet-process polyurethane resin includes three components: A, B, and C. By weight percentage, the preparation raw materials of the A component include the following components:
[0073]
[0074] By weight percentage, the preparation raw materials of the B component include the following components:
[0075]
[0076]
[0077] The C component is composed of cellulose acetate butyrate and SAN resin in a weight ratio of 1:2.
[0078] Wherein, the number-average molecular weight of polyethylene oxide diol is 2000g / mol, the number-average molecular weight of polyethylene adipate diol is 4000g / mol, and the number-average molecular weight of polycaprolactone diol is 2000g / mol, The number average molecular weight of the phthalic anhydride polyester diol is 2000 g / mol; the weight ratio of the A component and the B component is 1:9; the C component accounts for 3% of the total weight of the A component a...
Embodiment 3
[0084] In this embodiment, a wet-process polyurethane resin is provided. The wet-process polyurethane resin includes three components: A, B, and C. By weight percentage, the preparation raw materials of the A component include the following components:
[0085]
[0086] By weight percentage, the preparation raw materials of the B component include the following components:
[0087]
[0088] The C component is composed of cellulose acetate butyrate and SAN resin in a weight ratio of 1:2.
[0089] Wherein, the number-average molecular weight of polyethylene oxide diol is 1000g / mol, the number-average molecular weight of polybutylene adipate diol is 2000g / mol, and the number-average molecular weight of polycaprolactone diol is 2000g / mol, The number-average molecular weight of the phthalic anhydride polyester diol is 2000 g / mol; the weight ratio of the A component and the B component is 1:3; the C component accounts for 3% of the total weight of the A component and the B com...
PUM
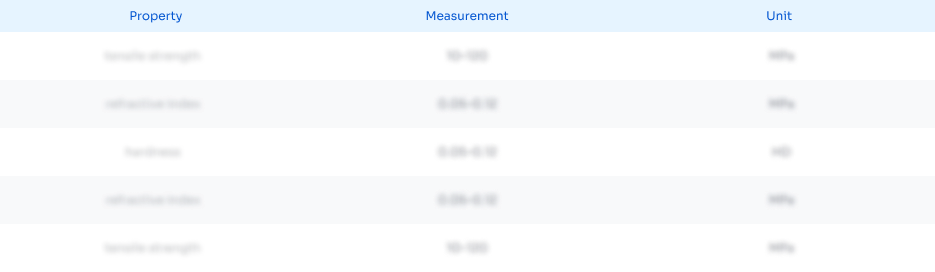
Abstract
Description
Claims
Application Information

- Generate Ideas
- Intellectual Property
- Life Sciences
- Materials
- Tech Scout
- Unparalleled Data Quality
- Higher Quality Content
- 60% Fewer Hallucinations
Browse by: Latest US Patents, China's latest patents, Technical Efficacy Thesaurus, Application Domain, Technology Topic, Popular Technical Reports.
© 2025 PatSnap. All rights reserved.Legal|Privacy policy|Modern Slavery Act Transparency Statement|Sitemap|About US| Contact US: help@patsnap.com