Manufacturing process of antibacterial mask
A production process and mask technology, which is applied in the field of antibacterial mask production process, can solve the problems of loss of antibacterial properties of masks, lack of protection against fine particles, and increased production costs
- Summary
- Abstract
- Description
- Claims
- Application Information
AI Technical Summary
Problems solved by technology
Method used
Examples
Embodiment 1
[0035] A kind of antibacterial mask manufacturing process, comprises the steps:
[0036] The first step, preparing antibacterial layer;
[0037] The second step, preparing activated carbon fiber layer;
[0038] The third step is to sew the non-woven fabric layer, activated carbon fiber layer, antibacterial layer, activated carbon fiber layer, and non-woven fabric layer stacked in sequence using hot-melt seam technology to make the cover body, and then sew the cover body and ear straps together Get up, equidistantly arrange several nose clip strips inside the edge-sealing cloth roll of the upper mouth, namely obtain a kind of antibacterial mask.
[0039] Further, the preparation process of the antibacterial layer is as follows:
[0040]Step S11, blending polylactic acid, polypropylene, sodium dodecylbenzenesulfonate and an antibacterial agent, and then extruding and granulating through a twin-screw extruder to obtain a blend, and the extrusion temperature is 230° C.;
[0041...
Embodiment 2
[0059] A kind of antibacterial mask manufacturing process, comprises the steps:
[0060] The first step, preparing antibacterial layer;
[0061] The second step, preparing activated carbon fiber layer;
[0062] The third step is to sew the non-woven fabric layer, activated carbon fiber layer, antibacterial layer, activated carbon fiber layer, and non-woven fabric layer stacked in sequence using hot-melt seam technology to make the cover body, and then sew the cover body and ear straps together Get up, equidistantly arrange several nose clip strips inside the edge-sealing cloth roll of the upper mouth, namely obtain a kind of antibacterial mask.
[0063] Further, the preparation process of the antibacterial layer is as follows:
[0064] Step S11, blending polylactic acid, polypropylene, sodium dodecylbenzenesulfonate and an antibacterial agent, and then extruding and granulating through a twin-screw extruder to obtain a blend, and the extrusion temperature is 230° C.;
[006...
Embodiment 3
[0083] A kind of antibacterial mask manufacturing process, comprises the steps:
[0084] The first step, preparing antibacterial layer;
[0085] The second step, preparing activated carbon fiber layer;
[0086] The third step is to sew the non-woven fabric layer, activated carbon fiber layer, antibacterial layer, activated carbon fiber layer, and non-woven fabric layer stacked in sequence using hot-melt seam technology to make the cover body, and then sew the cover body and ear straps together Get up, equidistantly arrange several nose clip strips inside the edge-sealing cloth roll of the upper mouth, namely obtain a kind of antibacterial mask.
[0087] Further, the preparation process of the antibacterial layer is as follows:
[0088] Step S11, blending polylactic acid, polypropylene, sodium dodecylbenzenesulfonate and an antibacterial agent, and then extruding and granulating through a twin-screw extruder to obtain a blend, and the extrusion temperature is 230° C.;
[008...
PUM
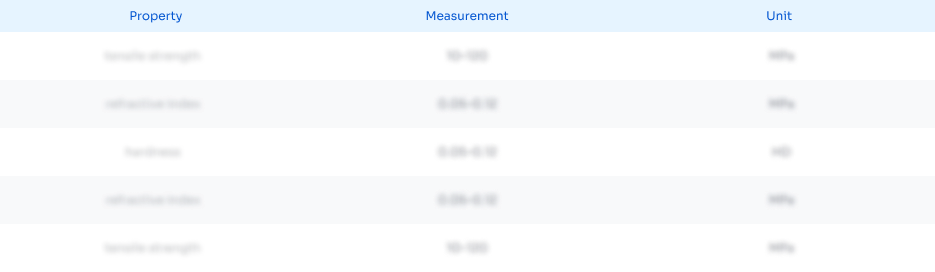
Abstract
Description
Claims
Application Information

- R&D Engineer
- R&D Manager
- IP Professional
- Industry Leading Data Capabilities
- Powerful AI technology
- Patent DNA Extraction
Browse by: Latest US Patents, China's latest patents, Technical Efficacy Thesaurus, Application Domain, Technology Topic, Popular Technical Reports.
© 2024 PatSnap. All rights reserved.Legal|Privacy policy|Modern Slavery Act Transparency Statement|Sitemap|About US| Contact US: help@patsnap.com