Preparation method of black glass batch smelted by electric melting furnace
A technology of black glass and batch materials, which is applied in the field of preparation of black glass batch materials, can solve the problems of refractory black glass, low production capacity, and high energy consumption, and achieve the effects of excellent glass quality, low raw material cost, and reduced pollution
- Summary
- Abstract
- Description
- Claims
- Application Information
AI Technical Summary
Problems solved by technology
Method used
Image
Examples
Embodiment
[0044] A method for preparing black glass batch materials suitable for melting in an electric melting furnace, mainly using waste daily-use bottles, glass utensils, various mineral raw materials and fluxing agents, adding an appropriate amount of oxidizing agent, clarifying agent, and coloring agent, using The method of electromelting produces black utensil glass, and in parts by weight, when batching, waste daily-use bottles and cans, utensil glass 11--15 parts, common sand 56--60 parts, potassium feldspar powder 9--12 Sodium boronite powder is 2-2.5 parts, zinc oxide is 0.2--0.4 parts, witherite powder is 0.3--0.5 parts, manganese powder is 2.7--3.5 parts, apatite powder is 0.6--1.0 parts, Chromium ore powder is 0.6--1.0 parts, soda ash is 10--12 parts, and cerium oxide is 0.15--0.3 parts.
[0045] As a further optimization of this scheme, in parts by weight, during batching, 11--15 parts of waste daily-use bottles, jars and utensils glass.
[0046] As a further optimizatio...
PUM
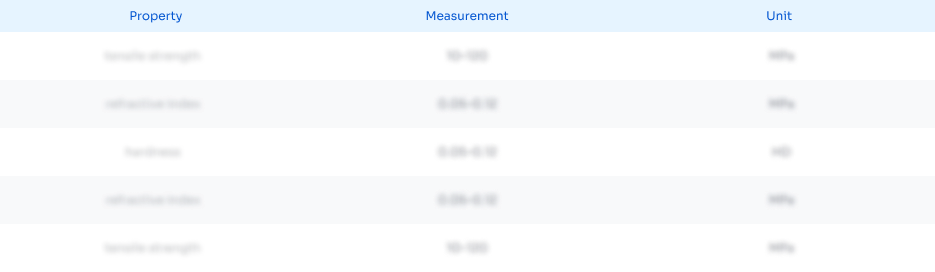
Abstract
Description
Claims
Application Information

- Generate Ideas
- Intellectual Property
- Life Sciences
- Materials
- Tech Scout
- Unparalleled Data Quality
- Higher Quality Content
- 60% Fewer Hallucinations
Browse by: Latest US Patents, China's latest patents, Technical Efficacy Thesaurus, Application Domain, Technology Topic, Popular Technical Reports.
© 2025 PatSnap. All rights reserved.Legal|Privacy policy|Modern Slavery Act Transparency Statement|Sitemap|About US| Contact US: help@patsnap.com