Manufacturing method of composite shear blade
A manufacturing method and alloy technology, applied in the direction of manufacturing tools, furnace types, furnaces, etc., can solve the problems of increasing the cost of cutting blades, increasing the brittleness tendency of materials, and inability to process assembly holes, so as to reduce the problem of product cracking and eliminate brittleness. , cost saving effect
- Summary
- Abstract
- Description
- Claims
- Application Information
AI Technical Summary
Problems solved by technology
Method used
Examples
Embodiment 1
[0043] A method of manufacturing a composite cutting edge suitable for cold rolling flying shears. The size of the cutting edge is 40mm*65mm*2030mm. The chemical composition and content of the material are:
[0044] element C Si mn Cr Mo V Cr12Mo1V1 1.4-1.6 ≤0.60 ≤0.60 11.0-13.0 0.7-1.2 0.5-1.1
[0045] Specific steps are as follows:
[0046] Step 1, making the blank:
[0047] According to the components and contents in the above table, high-alloy forging blanks are made, and 45# steel is used to make carbon steel forging blanks.
[0048] Step 2. Forging and compounding two materials:
[0049] According to the design size of the cutting edge and process two parts of the forging billet to keep the bright surface of the forging billet, weld the two parts of the forging billet together, and then adopt the high temperature forging method, heat it to 1160 ℃ forging, and forge the high alloy forging billet and carbon steel forging The billet is up...
Embodiment 2
[0059] A method of manufacturing a composite cutting edge suitable for hot rolling flying shears. The size of the cutting edge is 100mm*190mm*1550mm. The chemical composition and content of the material are:
[0060] element C Si mn Cr Mo V H13 material 0.4-0.7 0.8-1.2 0.2-0.5 4.75-5.50 1.1-1.75 0.8-1.2
[0061] Specific steps are as follows:
[0062] Step 1, making the blank:
[0063]According to the components and contents in the above table, high-alloy forging blanks are made, and 45# steel is used to make carbon steel forging blanks.
[0064] Step 2. Forging and compounding two materials:
[0065] According to the design size of the cutting edge and process two parts of the forging billet to keep the bright surface of the forging billet, weld the two parts of the forging billet together, and then use high temperature forging, heat to 1230 ° C forging, and forge the high alloy forging billet and carbon steel forging The billet is upsettin...
PUM
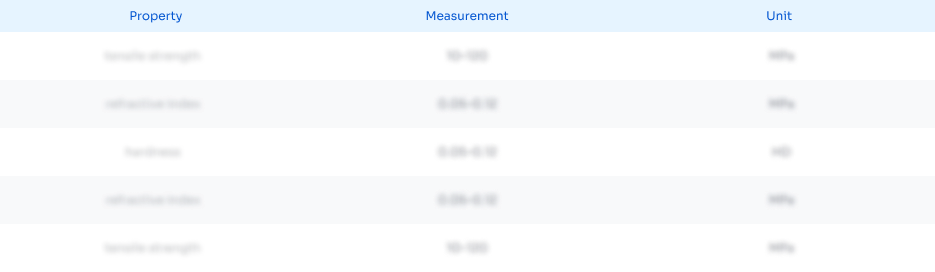
Abstract
Description
Claims
Application Information

- Generate Ideas
- Intellectual Property
- Life Sciences
- Materials
- Tech Scout
- Unparalleled Data Quality
- Higher Quality Content
- 60% Fewer Hallucinations
Browse by: Latest US Patents, China's latest patents, Technical Efficacy Thesaurus, Application Domain, Technology Topic, Popular Technical Reports.
© 2025 PatSnap. All rights reserved.Legal|Privacy policy|Modern Slavery Act Transparency Statement|Sitemap|About US| Contact US: help@patsnap.com