Preparation technology of high-hardness stainless steel
A preparation process, stainless steel technology, applied in the field of stainless steel, can solve the problems of low hardness of stainless steel, can not meet the special hardness requirements of products, etc.
- Summary
- Abstract
- Description
- Claims
- Application Information
AI Technical Summary
Problems solved by technology
Method used
Examples
Embodiment 1
[0025] A preparation process of high-hardness stainless steel, comprising the following steps:
[0026] 1) Mix 0.5 parts of carbon, 10 parts of chromium, 1.4 parts of manganese, 20 parts of copper, 1 part of silver, 1 part of silver, 20 parts of aluminum, 35 parts of iron, 14 parts of silicon and 6 parts The zinc raw materials are put into the smelting furnace together for smelting, and the argon gas is introduced when the temperature in the furnace reaches a certain temperature, so that the smelted molten steel is fully mixed with the argon gas. After the gas is fully mixed with the molten steel, impurities are precipitated and filtered to obtain pure molten steel;
[0027] 2) Pouring the pure molten steel obtained in step 1) to obtain a stainless steel slab, and annealing the stainless steel slab through an annealing furnace, the temperature in the annealing furnace is 700°C, the annealing time is controlled at 3 hours, and the annealing temperature is lower than 500°C Fina...
Embodiment 2
[0035] A preparation process of high-hardness stainless steel, comprising the following steps:
[0036] 1) Mix 0.85 parts of carbon, 13 parts of chromium, 1.5 parts of manganese, 25 parts of copper, 1.3 parts of silver, 1.3 parts of silver, 25 parts of aluminum, 37.5 parts of iron, 17 parts of silicon and 9 parts The zinc raw materials are put into the smelting furnace together for smelting, and the argon gas is introduced when the temperature in the furnace reaches a certain temperature, so that the smelted molten steel is fully mixed with the argon gas, and the time of argon gas feeding is controlled within 5 minutes, so that After the gas is fully mixed with the molten steel, impurities are precipitated and filtered to obtain pure molten steel;
[0037] 2) Pouring the pure molten steel obtained in step 1) to obtain a stainless steel slab, and annealing the stainless steel slab through an annealing furnace, the temperature in the annealing furnace is 800°C, the annealing tim...
Embodiment 3
[0045] A preparation process of high-hardness stainless steel, comprising the following steps:
[0046] 1) Mix 1.2 parts of carbon, 16 parts of chromium, 1.6 parts of manganese, 30 parts of copper, 1.6 parts of silver, 1.6 parts of silver, 30 parts of aluminum, 40 parts of iron, 20 parts of silicon and 12 parts The zinc raw materials are put into the smelting furnace together for smelting, and the argon gas is introduced when the temperature in the furnace reaches a certain temperature, so that the smelted molten steel is fully mixed with the argon gas. After the gas is fully mixed with the molten steel, impurities are precipitated and filtered to obtain pure molten steel;
[0047] 2) Pouring the pure molten steel obtained in step 1) to obtain a stainless steel slab, and annealing the stainless steel slab through an annealing furnace, the temperature in the annealing furnace is 900°C, the annealing time is controlled at 5 hours, and the annealing temperature is lower than 500°...
PUM
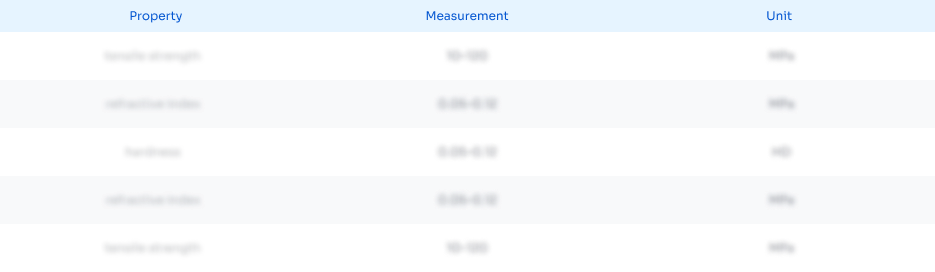
Abstract
Description
Claims
Application Information

- R&D Engineer
- R&D Manager
- IP Professional
- Industry Leading Data Capabilities
- Powerful AI technology
- Patent DNA Extraction
Browse by: Latest US Patents, China's latest patents, Technical Efficacy Thesaurus, Application Domain, Technology Topic, Popular Technical Reports.
© 2024 PatSnap. All rights reserved.Legal|Privacy policy|Modern Slavery Act Transparency Statement|Sitemap|About US| Contact US: help@patsnap.com