Automatic carrying system based on AGVs and multi-AGV cooperation method
A handling system and automatic technology, applied in vibration suppression adjustment, lifting device, spring/shock absorber, etc., can solve the problems of limited detection range and self-reaction ability of automatic handling equipment, large amount of automatic handling equipment, etc. Efficiency, improve stability, avoid the effect of idle waste
- Summary
- Abstract
- Description
- Claims
- Application Information
AI Technical Summary
Problems solved by technology
Method used
Image
Examples
Embodiment Construction
[0044] The following will clearly and completely describe the technical solutions in the embodiments of the present invention with reference to the accompanying drawings in the embodiments of the present invention. Obviously, the described embodiments are only some, not all, embodiments of the present invention. Based on the embodiments of the present invention, all other embodiments obtained by persons of ordinary skill in the art without creative efforts fall within the protection scope of the present invention.
[0045] see Figure 1-9 , the present embodiment discloses an automatic handling system based on AGV, comprising an AGV carrier body 1, a driving wheel 2 is arranged on the lower chassis of the AGV carrier body 1, and a side of the AGV carrier body 1 along the forward direction is provided with The platform 3 is carried, and the suspension wheel 4 is provided at the position corresponding to the drive wheel 2 under the main body of the AGV carrier 1, and the opposit...
PUM
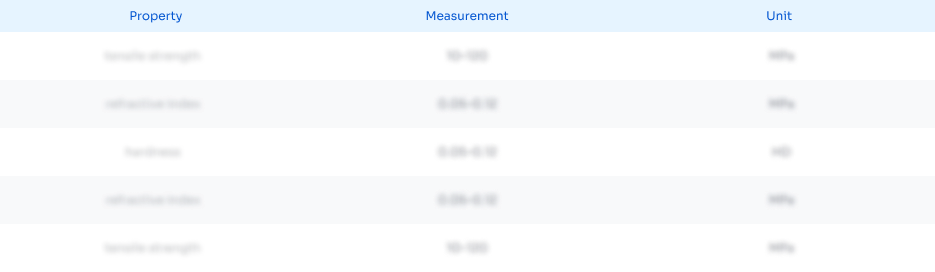
Abstract
Description
Claims
Application Information

- R&D
- Intellectual Property
- Life Sciences
- Materials
- Tech Scout
- Unparalleled Data Quality
- Higher Quality Content
- 60% Fewer Hallucinations
Browse by: Latest US Patents, China's latest patents, Technical Efficacy Thesaurus, Application Domain, Technology Topic, Popular Technical Reports.
© 2025 PatSnap. All rights reserved.Legal|Privacy policy|Modern Slavery Act Transparency Statement|Sitemap|About US| Contact US: help@patsnap.com