Aero-engine blade robot autonomous measurement method and system
A technology of aero-engines and measurement methods, which is applied in the direction of measuring devices, instruments, and optical devices, and can solve problems such as low detection efficiency and complex measurement path planning
- Summary
- Abstract
- Description
- Claims
- Application Information
AI Technical Summary
Problems solved by technology
Method used
Image
Examples
Embodiment Construction
[0087] In order to make the technical solution of the present invention clearer and clearer to those skilled in the art, the present invention will be described in further detail below in conjunction with the embodiments and accompanying drawings. The features in the example can be combined with each other.
[0088] refer to figure 1 , figure 1 An autonomous measurement method for an aeroengine blade robot provided in this embodiment includes the following steps:
[0089] S1: Calibrate the servo rotary table 1, the structured light 3D scanner 4 and the robot 5;
[0090] S2: Arrange measurement points according to the design model of the aeroengine blade;
[0091] S3: planning the path measured by the robot 5;
[0092] S4: Measure the three-dimensional shape of the aeroengine blade;
[0093] S5: Process the measurement data of the aeroengine blade.
[0094] Further, refer to figure 2 , the calibration of the servo rotary table 1, the structured light three-dimensional s...
PUM
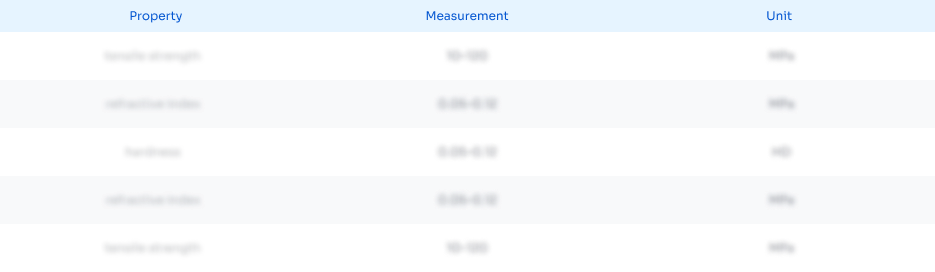
Abstract
Description
Claims
Application Information

- R&D Engineer
- R&D Manager
- IP Professional
- Industry Leading Data Capabilities
- Powerful AI technology
- Patent DNA Extraction
Browse by: Latest US Patents, China's latest patents, Technical Efficacy Thesaurus, Application Domain, Technology Topic, Popular Technical Reports.
© 2024 PatSnap. All rights reserved.Legal|Privacy policy|Modern Slavery Act Transparency Statement|Sitemap|About US| Contact US: help@patsnap.com