Method for preparing degradable plastic master batch from soluble salt assisted plasticized amylose
A technology for plasticizing straight-chain and degradable plastics, which is applied in the field of degradable plastic masterbatches. It can solve the problems of reduced strength of thermoplastic starch, high straight-chain content, and inapplicability of pea starch, and achieve stable thermoplasticity, prevent recrystallization, and good thermoplasticity. Effect
- Summary
- Abstract
- Description
- Claims
- Application Information
AI Technical Summary
Problems solved by technology
Method used
Image
Examples
Embodiment 1
[0035] A kind of preparation of the method that soluble salt assists plasticized amylose to prepare degradable plastic masterbatch:
[0036] (1) Make a slurry by mixing Xingxing brand pea starch amylose from Gansu Xingxing Starch Food Co., Ltd. with sodium chloride soluble salt and water according to the mass ratio of 20:7:60, and place it in a stirring pot at 85-90°C Stir slowly and gelatinize to obtain starch gelatinized slurry for subsequent use;
[0037] (2) Combine the starch gelatinization slurry in step (1) with ethylene glycol plasticizer and polyadipate-1,4-butylene glycol ester diol with an average molecular weight of 2000 in a mass ratio of 100:3:4 Kneading, vacuuming and draining at 80°C to form pre-plasticized starch;
[0038] (3) Add the pre-plasticized starch (2) into the reactor, feed nitrogen into the reactor, add diphenylmethane-4.4'-diisocyanate at the same time, slowly stir and react at 80°C for 25 minutes, and then send the reaction material into the scre...
Embodiment 2
[0041] A kind of preparation of the method that soluble salt assists plasticized amylose to prepare degradable plastic masterbatch:
[0042] (1) Mix the Xingxing brand pea starch amylose from Gansu Xingxing Starch Food Co., Ltd. with calcium gluconate soluble salt and water to make a slurry according to the mass ratio of 24:7:60, and place it in a stirring pot at 80-85°C Stir slowly and gelatinize to obtain starch gelatinized slurry for subsequent use;
[0043] (2) Combine the starch gelatinization slurry in step (1) with ethylene glycol plasticizer and polyadipate-1,4-butylene glycol ester diol with an average molecular weight of 2000 according to the mass ratio of 100:4:4 Kneading, vacuuming and draining at 80°C to form pre-plasticized starch;
[0044] (3) Add the pre-plasticized starch (2) into the reactor, feed nitrogen into the reactor, add diphenylmethane-4.4'-diisocyanate at the same time, slowly stir and react at 80°C for 25 minutes, and then send the reaction materia...
Embodiment 3
[0047] A kind of preparation of the method that soluble salt assists plasticized amylose to prepare degradable plastic masterbatch:
[0048] (1). Make a slurry by mixing Xingxing brand pea starch amylose from Gansu Xingxing Starch Food Co., Ltd. with zinc acetate soluble salt and water according to the mass ratio of 28:7:80, and place it in a stirring pot at 80-90°C Stir slowly and gelatinize to obtain starch gelatinized slurry for subsequent use;
[0049] (2). The step (1) starch gelatinization slurry and ethylene glycol plasticizer, the average molecular weight is 2000 polyadipate-1,4-butylene glycol ester diol according to the mass ratio of 100:3:5 Carry out kneading, vacuumize and drain water at 80°C to form pre-plasticized starch;
[0050] (3). Add the pre-plasticized starch (2) into the reaction kettle, feed nitrogen into the reaction kettle, add diphenylmethane-4.4'-diisocyanate at the same time, slowly stir and react at 80°C for 25min, and then send the reaction mater...
PUM
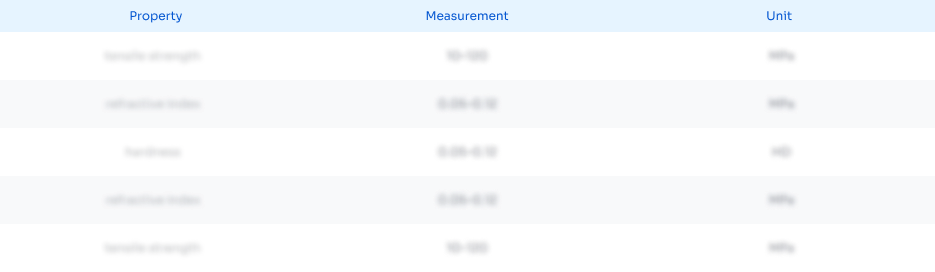
Abstract
Description
Claims
Application Information

- R&D
- Intellectual Property
- Life Sciences
- Materials
- Tech Scout
- Unparalleled Data Quality
- Higher Quality Content
- 60% Fewer Hallucinations
Browse by: Latest US Patents, China's latest patents, Technical Efficacy Thesaurus, Application Domain, Technology Topic, Popular Technical Reports.
© 2025 PatSnap. All rights reserved.Legal|Privacy policy|Modern Slavery Act Transparency Statement|Sitemap|About US| Contact US: help@patsnap.com