Corrosion-resistant plastic and preparation method thereof
A corrosion-resistant and plastic technology, applied in the field of corrosion-resistant plastics and their preparation, can solve the problems of plastic performance decline, plastic service life reduction, and self-performance reduction, etc., to increase corrosion resistance, increase service life, and improve corrosion resistance. Effect
- Summary
- Abstract
- Description
- Claims
- Application Information
AI Technical Summary
Problems solved by technology
Method used
Image
Examples
Embodiment 1
[0041] A corrosion-resistant plastic, made of the following raw materials in parts by weight: 80 parts of polyvinyl chloride, 5 parts of corrosion-resistant filler, 1 part of cadmium stearate, 3 parts of diethyl phthalate, and 3 parts of heat stabilizer;
[0042] The corrosion-resistant plastic is made by the following steps:
[0043] Step S1: Stir the polyvinyl chloride and cadmium stearate for 10 minutes at a rotating speed of 300 r / min to obtain the first mixture;
[0044] Step S2: Stir the corrosion-resistant filler and heat stabilizer at a rotational speed of 500 r / min for 3 minutes, then add diethyl phthalate, and continue stirring for 10 minutes to obtain a second mixture;
[0045] Step S3: melting and stirring the first mixture and the second mixture for 30 minutes under the conditions of a rotation speed of 1000 r / min and a temperature of 170° C. to obtain a molten material;
[0046] Step S4: Put the molten material into a three-stage twin-screw extruder, extrude and...
Embodiment 2
[0058] A corrosion-resistant plastic, made of the following raw materials in parts by weight: 90 parts of polyvinyl chloride, 6 parts of corrosion-resistant filler, 2 parts of cadmium stearate, 4 parts of diethyl phthalate, and 4 parts of heat stabilizer;
[0059] The corrosion-resistant plastic is made by the following steps:
[0060] Step S1: stirring the polyvinyl chloride and cadmium stearate for 15 minutes at a rotational speed of 300 r / min to obtain the first mixture;
[0061] Step S2: Stir the corrosion-resistant filler and heat stabilizer at a rotational speed of 500 r / min for 5 minutes, then add diethyl phthalate, and continue stirring for 10 minutes to obtain a second mixture;
[0062] Step S3: melting and stirring the first mixture and the second mixture for 40 minutes under the conditions of a rotation speed of 1200 r / min and a temperature of 170° C. to obtain a molten material;
[0063] Step S4: Put the molten material into a three-stage twin-screw extruder, extr...
Embodiment 3
[0075] A corrosion-resistant plastic, made of the following raw materials in parts by weight: 100 parts of polyvinyl chloride, 8 parts of corrosion-resistant filler, 3 parts of cadmium stearate, 5 parts of diethyl phthalate, and 5 parts of heat stabilizer;
[0076] The corrosion-resistant plastic is made by the following steps:
[0077] Step S1: stirring the polyvinyl chloride and cadmium stearate for 15 minutes at a rotating speed of 500 r / min to obtain the first mixture;
[0078] Step S2: Stir the corrosion-resistant filler and heat stabilizer at a rotational speed of 800 r / min for 5 minutes, then add diethyl phthalate, and continue stirring for 15 minutes to obtain a second mixture;
[0079] Step S3: melting and stirring the first mixture and the second mixture for 40 minutes at a rotation speed of 1200 r / min and a temperature of 190° C. to obtain a molten material;
[0080] Step S4: Put the molten material into a three-stage twin-screw extruder, extrude and cool and pelle...
PUM
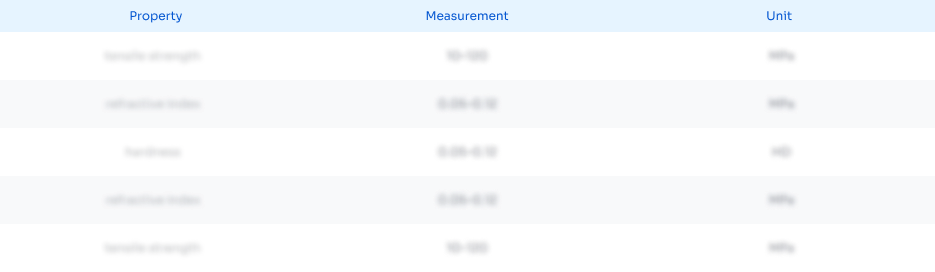
Abstract
Description
Claims
Application Information

- R&D Engineer
- R&D Manager
- IP Professional
- Industry Leading Data Capabilities
- Powerful AI technology
- Patent DNA Extraction
Browse by: Latest US Patents, China's latest patents, Technical Efficacy Thesaurus, Application Domain, Technology Topic, Popular Technical Reports.
© 2024 PatSnap. All rights reserved.Legal|Privacy policy|Modern Slavery Act Transparency Statement|Sitemap|About US| Contact US: help@patsnap.com