Thermal radiation type energy-saving and environment-friendly scrap steel preheating system
An energy-saving, environmental-friendly, heat-radiating technology, applied to preheating costs, lighting and heating equipment, furnaces, etc., can solve the problems of uneven heat conduction, difficult cleaning, and high equipment investment costs, so as to save consumption, improve heat utilization rate, The effect of shortening the smelting time
- Summary
- Abstract
- Description
- Claims
- Application Information
AI Technical Summary
Problems solved by technology
Method used
Image
Examples
Embodiment Construction
[0027] As shown in the attached figure, the thermal radiation energy-saving and environment-friendly scrap steel preheating system includes a horizontal preheating conveying mechanism and a vertical preheating conveying mechanism, and the vertical preheating conveying mechanism is connected with the horizontal preheating conveying mechanism. By setting the connected vertical preheating conveying mechanism and horizontal preheating conveying mechanism, the horizontal preheating conveying mechanism is connected with the melting electric furnace, and the high temperature gas generated during electric furnace smelting first flows backward through the horizontal preheating conveying mechanism, and then passes through the horizontal The preheating conveying mechanism enters into the vertical preheating conveying mechanism connected with the horizontal preheating conveying mechanism for preheating. By first entering the horizontal preheating conveying mechanism, the steel scrap enters...
PUM
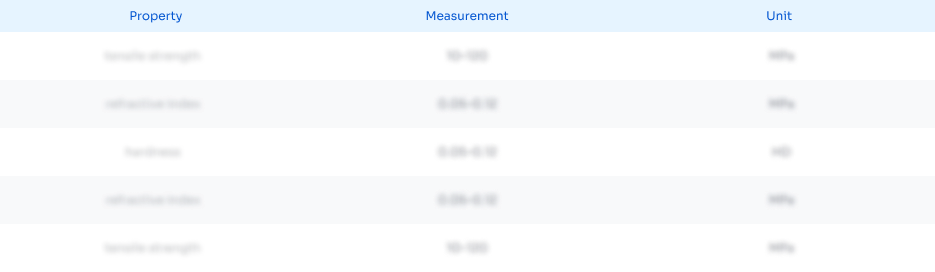
Abstract
Description
Claims
Application Information

- R&D
- Intellectual Property
- Life Sciences
- Materials
- Tech Scout
- Unparalleled Data Quality
- Higher Quality Content
- 60% Fewer Hallucinations
Browse by: Latest US Patents, China's latest patents, Technical Efficacy Thesaurus, Application Domain, Technology Topic, Popular Technical Reports.
© 2025 PatSnap. All rights reserved.Legal|Privacy policy|Modern Slavery Act Transparency Statement|Sitemap|About US| Contact US: help@patsnap.com