Nitriding treatment method for aluminum profile extrusion die
A technology of extrusion die and nitriding treatment, applied in metal material coating process, coating, solid-state diffusion coating, etc. The effect of nitriding layer spalling
- Summary
- Abstract
- Description
- Claims
- Application Information
AI Technical Summary
Problems solved by technology
Method used
Image
Examples
Embodiment 1
[0012] Carry out nitriding treatment in Φ2.2×4.5m gas nitriding furnace for 8 Φ280mm molds with steel grade H13 that have been processed to finished products. Heat at 520°C for 15 hours, control the ammonia decomposition rate in the furnace to 20%, then continue heating to 540°C for 8 hours, control the ammonia decomposition rate in the furnace to 45%, stop passing ammonia gas after 8 hours at 540°C, Add 50g of rare earth La blocks into the furnace, pass argon into the furnace, lower the furnace temperature to 460°C and keep it for 3 hours, then cool it down to 200°C at a rate of 50°C / h before taking it out of the furnace.
Embodiment 2
[0014] Carry out nitriding treatment on 6 Φ320mm molds with steel grade H13 that have been processed to finished products in a Φ2.2×4.5m gas nitriding furnace. Keep warm at 500°C for 20 hours, control the ammonia decomposition rate in the furnace to 30%, then continue heating to 550°C for 5 hours, control the ammonia decomposition rate in the furnace to 50%, stop passing ammonia after 5 hours at 550°C, Add 50g of rare earth La blocks into the furnace, pass argon gas into the furnace, lower the furnace temperature to 480°C and keep it for 2 hours, then cool it down to 200°C at a rate of 50°C / h before taking it out of the furnace.
Embodiment 3
[0016] Nitriding treatment was carried out on 5 Φ460mm finished molds with steel grade H13 in a Φ2.2×4.5m gas nitriding furnace. Before heating up, pass ammonia to exhaust and heat at a heating rate of 50°C / h. Keep warm at 510°C for 18 hours, control the ammonia decomposition rate in the furnace to 25%, then continue heating to 530°C for 10 hours, control the ammonia decomposition rate in the furnace to 40%, stop the ammonia gas after 10 hours at 530°C, Add 50g of rare earth La blocks into the furnace, pass argon gas into the furnace, lower the furnace temperature to 460°C and keep it for 4 hours, then cool it down to 200°C at a rate of 50°C / h before taking it out of the furnace.
PUM
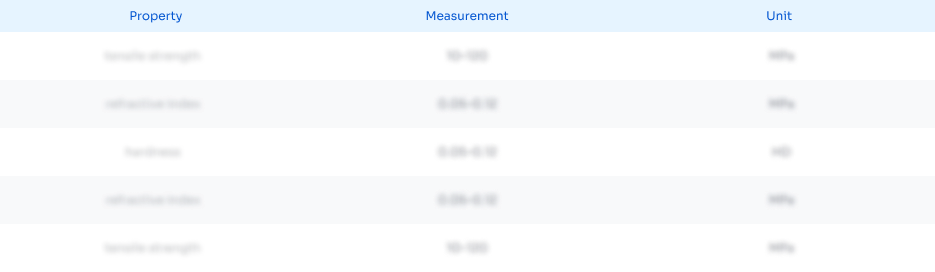
Abstract
Description
Claims
Application Information

- R&D Engineer
- R&D Manager
- IP Professional
- Industry Leading Data Capabilities
- Powerful AI technology
- Patent DNA Extraction
Browse by: Latest US Patents, China's latest patents, Technical Efficacy Thesaurus, Application Domain, Technology Topic, Popular Technical Reports.
© 2024 PatSnap. All rights reserved.Legal|Privacy policy|Modern Slavery Act Transparency Statement|Sitemap|About US| Contact US: help@patsnap.com