Method for extracting titanium and reducing impurities from vanadium titano-magnetite iron ore dressing tailings
A vanadium-titanium magnetite and tailings technology, which is applied to chemical instruments and methods, flotation, magnetic separation, etc., can solve the problems of deteriorating flotation indicators, loss of titanium resources, and high lower limit of sorting particle size, and achieve improved flotation Efficiency and indicators, reducing resource waste, reducing the effect of process flow
- Summary
- Abstract
- Description
- Claims
- Application Information
AI Technical Summary
Problems solved by technology
Method used
Image
Examples
Embodiment 1
[0041] Such as figure 1Shown, a kind of vanadium-titanium-magnetite iron-separating tailings is carried out the method for removing titanium and impurities, and the vanadium-titanium-magnetite iron-separating tailings in the present embodiment belongs to the low-grade vanadium-titanium-magnetite of high magnesium, high calcium and iron In iron ore tailings, the titanium minerals are mainly ilmenite, followed by titanite; the content of iron minerals is low, mostly titanomagnetite, and a small amount of magnetite, hematite and limonite can also be seen; Metal sulfides are dominated by pyrrhotite, followed by pyrite, and occasionally sulfur cobalt ore; non-metallic minerals with relatively high content are plagioclase, titanopyroxene and chlorite, followed by titanium amphibole, etc. The grain size of ilmenite crystals is mostly between 0.01-0.15mm, including the following steps:
[0042] (1) The vanadium-titanium magnetite iron beneficiation tailings (fineness -200 mesh accoun...
PUM
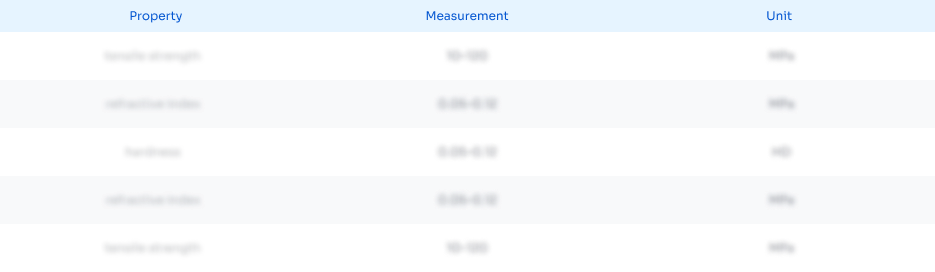
Abstract
Description
Claims
Application Information

- Generate Ideas
- Intellectual Property
- Life Sciences
- Materials
- Tech Scout
- Unparalleled Data Quality
- Higher Quality Content
- 60% Fewer Hallucinations
Browse by: Latest US Patents, China's latest patents, Technical Efficacy Thesaurus, Application Domain, Technology Topic, Popular Technical Reports.
© 2025 PatSnap. All rights reserved.Legal|Privacy policy|Modern Slavery Act Transparency Statement|Sitemap|About US| Contact US: help@patsnap.com