Preparation method and application of acid-process cold core box resin for casting
A technology of cold box and resin, which is applied to casting molding equipment, molds, cores, etc., which can solve the problems of burrs, poisonous triethylamine, and poor surface quality of castings, so as to improve strength, reduce harmful components, and improve production efficiency. high efficiency effect
- Summary
- Abstract
- Description
- Claims
- Application Information
AI Technical Summary
Problems solved by technology
Method used
Image
Examples
Embodiment 1
[0019] The first step, weigh the following raw materials according to the parts by weight: 42 parts of modified benzoxazine resin, 33 parts of chloroether resin, 15 parts of L-lysine diisocyanate, 22 parts of maleic anhydride, polyester resin 11 parts of softening agent, 3 parts of catalyst dibenzoyl peroxide and 1 part of sand surface modifier 2-methacrylic acid chromium chloride; the second step, resin slurry: add chlorine ether resin and maleic anhydride In the pulverizer, pulverize for 30 minutes, then pour the mixture into a high-speed mixer, add diisocyanate, catalyst, and polyester resin softener into the high-speed mixer according to the formula, and fully stir for 10 minutes to obtain a resin slurry; the third step , the resin slurry and the modified benzoxazine resin are fully mixed and stirred evenly to obtain final product. The preparation method of the modified benzoxazine is as follows: 12.8 parts of phenol, 8 parts of paraformaldehyde and 18 parts of 4- 01.1 par...
Embodiment 2
[0023]The first step, weigh the following raw materials according to the parts by weight: 39 parts of modified benzoxazine resin, 31 parts of chloroether resin, 13 parts of toluene diisocyanate, 19 parts of maleic anhydride, 9 parts of polyester resin softener , 1 part of catalyst azobisisobutyronitrile and 0.5 part of sand surface modifier vinyl benzyl aminoethyl trimethoxysilane hydrochloride; the second step, resin slurry: dichloroether resin, maleic butene di Add the acid anhydride into the pulverizer, pulverize for 20 minutes, then pour the mixture into a high-speed mixer, add diisocyanate, catalyst, and polyester resin softener into the high-speed mixer according to the formula, and fully stir for 10 minutes to obtain a resin slurry; Three steps, the resin slurry and the modified benzoxazine resin are fully mixed and stirred evenly, and the preparation method of the modified benzoxazine is as follows: 11.5 parts of phenol, 7 parts of paraformaldehyde and 17 parts of 0.6 ...
PUM
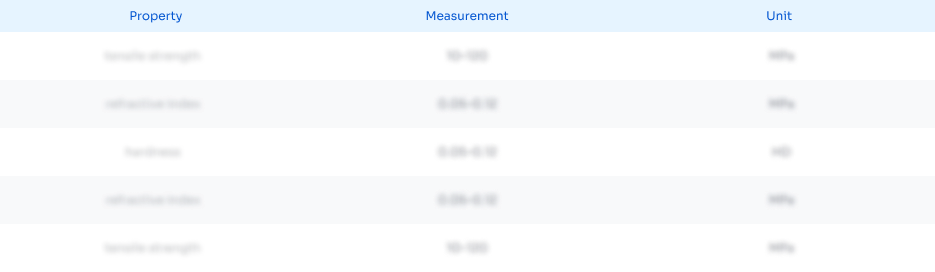
Abstract
Description
Claims
Application Information

- R&D
- Intellectual Property
- Life Sciences
- Materials
- Tech Scout
- Unparalleled Data Quality
- Higher Quality Content
- 60% Fewer Hallucinations
Browse by: Latest US Patents, China's latest patents, Technical Efficacy Thesaurus, Application Domain, Technology Topic, Popular Technical Reports.
© 2025 PatSnap. All rights reserved.Legal|Privacy policy|Modern Slavery Act Transparency Statement|Sitemap|About US| Contact US: help@patsnap.com