Cu-Fe bimetallic oxide material as well as preparation method and application thereof
A double metal oxide, cu-fe technology, applied in the field of materials, can solve the problems of inconvenient application, low conductivity, low energy density, etc.
- Summary
- Abstract
- Description
- Claims
- Application Information
AI Technical Summary
Problems solved by technology
Method used
Image
Examples
Embodiment 1
[0057] (1) Solution A in the preparation of Cu-Fe-PBAs:
[0058] Dissolve 0.4mmol (0.1317g) of potassium ferricyanide in 20mL of deionized water to form a uniform golden transparent solution A;
[0059] (2) Solution B in the preparation of Cu-Fe-PBAs
[0060] Completely dissolve 1g of polyvinylpyrrolidone in 20mL of deionized water, then add 0.6mmol (0.1499g) of copper sulfate powder and 0.9mmol (0.2647g) of trisodium citrate, and stir evenly to dissolve into a transparent solution B;
[0061] (3) Add solution B to solution A drop by drop through a rubber dropper, and mix completely. After standing for 24 hours, pour off the supernatant, collect the lower precipitate (ie Cu-Fe-PBAs precursor), and precipitate water alcohol After washing, it was vacuum-dried at 60°C and ground into powder.
[0062] (4) Evenly disperse the dry powder in the porcelain boat, put it into the muffle furnace and calcinate at 400°C for 1 hour to obtain CuFeO 8 Complex.
Embodiment 2
[0064] (1) Solution A in the preparation of Cu-Fe-PBAs:
[0065] Dissolve 0.6mmol (0.3951g) of potassium ferricyanide in 20mL of deionized water to form a uniform golden transparent solution A;
[0066] (2) Solution B in the preparation of Cu-Fe-PBAs
[0067] Completely dissolve 1g of polyvinylpyrrolidone in 20mL of deionized water, then add 0.4mmol (0.0999g) of copper sulfate powder and 0.9mmol (0.2647g) of trisodium citrate, and stir evenly to dissolve into a transparent solution B;
[0068] (3) Add solution B to solution A drop by drop through a rubber dropper, and mix completely. After standing for 24 hours, pour off the supernatant, collect the lower precipitate (ie Cu-Fe-PBAs precursor), and precipitate water alcohol After washing, it was vacuum-dried at 60°C and ground into powder.
[0069] (4) Disperse the dried powder evenly in a porcelain boat, put it into a muffle furnace and calcinate at 400°C for 1 hour to obtain CuFe-O 2 Complex.
Embodiment 3
[0071] (1) Solution A in the preparation of Cu-Fe-PBAs:
[0072] Dissolve 0.6mmol (0.3951g) of potassium ferricyanide in 20mL of deionized water to form a uniform golden transparent solution A;
[0073] (2) Solution B in the preparation of Cu-Fe-PBAs
[0074] Completely dissolve 1g of polyvinylpyrrolidone in 20mL of deionized water, then add 0.4mmol (0.0999g) of copper sulfate powder and 0.9mmol (0.2647g) of trisodium citrate, and stir evenly to dissolve into a transparent solution B;
[0075] (3) Add solution B to solution A drop by drop through a rubber dropper, and mix completely. After standing for 24 hours, pour off the supernatant, collect the lower precipitate (ie Cu-Fe-PBAs precursor), and precipitate water alcohol After washing, it was vacuum-dried at 60°C and ground into powder.
[0076] (4) Evenly disperse the dry powder in the porcelain boat, put it into the muffle furnace and calcinate at 500°C for 1h to obtain CuFe-O 2 Complex.
PUM
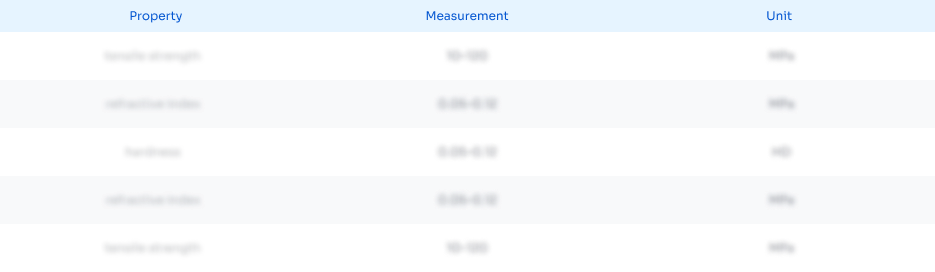
Abstract
Description
Claims
Application Information

- R&D
- Intellectual Property
- Life Sciences
- Materials
- Tech Scout
- Unparalleled Data Quality
- Higher Quality Content
- 60% Fewer Hallucinations
Browse by: Latest US Patents, China's latest patents, Technical Efficacy Thesaurus, Application Domain, Technology Topic, Popular Technical Reports.
© 2025 PatSnap. All rights reserved.Legal|Privacy policy|Modern Slavery Act Transparency Statement|Sitemap|About US| Contact US: help@patsnap.com