Preparation process of biodegradable resin-based composite material
A biodegradable resin and composite material technology, applied in the field of biodegradable resin-based composite material preparation technology, can solve the problems of poor high temperature resistance, high temperature resistance, etc. The effect of reducing preparation time
- Summary
- Abstract
- Description
- Claims
- Application Information
AI Technical Summary
Problems solved by technology
Method used
Image
Examples
Embodiment 1
[0026] The invention provides a preparation process of a biodegradable resin-based composite material, which specifically includes the following steps:
[0027] Step 1: Add 130 parts of epoxy resin, 180 parts of phenolic resin, and 100 parts of silicone resin into the stirring furnace, wait for the temperature of the stirring furnace to rise to 330°C, and then stir at a speed of 65 rpm for 60 minutes until the material is fully uniform After mixing, the stirring was stopped, the temperature in the stirring furnace was kept at 300° C., and the mixture was allowed to stand for 30 minutes to obtain material A.
[0028] Step 2: Take 0.6 parts of ferric chloride and 1 part of shrinkage additive, vacuum dehydrate at 100°C, then add to material A, add 130 parts of polyacid milk at the same time, stir for 30-50 minutes, and make it fully mixed , to obtain material B.
[0029] Step 3: Pour 130 parts of bismaleimide and 100 parts of cyanate resin into material B, and stir at a speed of...
Embodiment 2
[0036] A preparation process of a biodegradable resin-based composite material, specifically comprising the following steps:
[0037] Step 1: Add 140 parts of epoxy resin, 190 parts of phenolic resin, and 100 parts of silicone resin into the stirring furnace, wait for the temperature of the stirring furnace to rise to 340°C, then stir at a speed of 70 rpm for 65 minutes, and wait until the material is fully After uniform mixing, the stirring was stopped, the temperature in the stirring furnace was kept at 300° C., and the mixture was allowed to stand for 30 minutes to obtain material A.
[0038] Step 2: Take 0.6 parts of ferric chloride and 1 part of shrinkage additive, vacuum dehydrate at 100°C, then add to material A, add 130 parts of polyacid milk at the same time, stir for 30-50 minutes, and make it fully mixed , to obtain material B.
[0039] Step 3: Pour 135 parts of bismaleimide and 110 parts of cyanate resin into material B, and stir at a speed of 160 rpm for 25 minut...
Embodiment 3
[0046] A preparation process for a biodegradable resin-based composite material, specifically comprising the following steps:
[0047] Step 1: Add 150 parts of epoxy resin, 195 parts of phenolic resin, and 110 parts of silicone resin into the stirring furnace, wait for the temperature of the stirring furnace to rise to 340°C, then stir at a speed of 70 rpm for 66 minutes, and wait until the material is fully After uniform mixing, the stirring was stopped, the temperature in the stirring furnace was kept at 300° C., and the mixture was allowed to stand for 30 minutes to obtain material A.
[0048] Step 2: Take 0.6 parts of ferric chloride and 1 part of shrinkage additive, vacuum dehydrate at 100°C, then add to material A, add 130 parts of polyacid milk at the same time, stir for 30-50 minutes, and make it fully mixed , to obtain material B.
[0049] Step 3: Pour 140 parts of bismaleimide and 115 parts of cyanate resin into material B, and stir at a speed of 160 rpm for 26 minu...
PUM
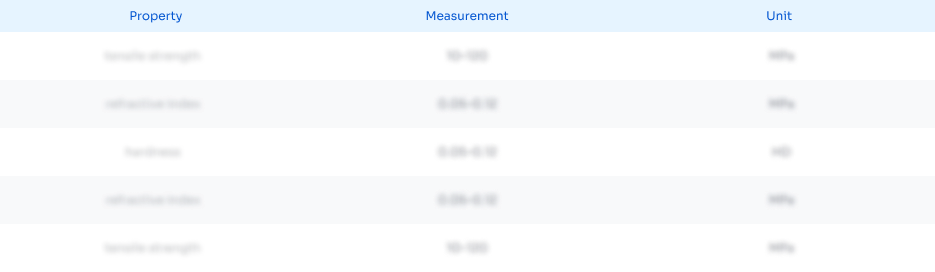
Abstract
Description
Claims
Application Information

- R&D
- Intellectual Property
- Life Sciences
- Materials
- Tech Scout
- Unparalleled Data Quality
- Higher Quality Content
- 60% Fewer Hallucinations
Browse by: Latest US Patents, China's latest patents, Technical Efficacy Thesaurus, Application Domain, Technology Topic, Popular Technical Reports.
© 2025 PatSnap. All rights reserved.Legal|Privacy policy|Modern Slavery Act Transparency Statement|Sitemap|About US| Contact US: help@patsnap.com