Method for preparing aluminum oxide coating by modulating high-current pulsed arc
A technology of alumina coating and strong current pulse, applied in coating, metal material coating process, vacuum evaporation coating, etc., can solve the problem of poor surface conductivity of target material, aggregation of aluminum arc spot movement, affecting coating quality, etc. The problem is to reduce the generation of large particles, improve the ionization rate, and increase the utilization rate.
- Summary
- Abstract
- Description
- Claims
- Application Information
AI Technical Summary
Problems solved by technology
Method used
Image
Examples
Embodiment 1
[0066] Embodiment 1, the aluminum oxide coating that utilizes pulsed arc technology to prepare on the cutting tool
[0067] Explanation: In this example, the binary nitride AlTiN is used as the base layer, and an aluminum oxide coating is deposited on the base again, and then TiN is deposited as a decorative functional layer.
[0068] The coating equipment used in the present invention is with the equipment size of routine industrial application: diameter D=1m, the equipment of height H=1m, carries out coating preparation, adopts conventional octahedron structure to carry out equipment description, is equipped with on the equipment Four rows of arcs, each row of arcs has 3 cathode arc sources.
[0069] see image 3 Shown: the first column is equipped with 3 Ti targets, the second column is equipped with 3 AlTi (40 / 60) targets, the third column is equipped with 3 pure metal Al targets, and the fourth column is equipped with 3 AlTi (50 / 60) targets 50).
[0070] Referring to t...
Embodiment 2
[0079] Embodiment two, the composite coating that utilizes pulsed arc technology to prepare on the cutting tool
[0080] Explanation: In this example, the ternary nitride AlTiCrN is used as the base layer, and a composite coating containing an aluminum oxide coating is deposited on the basis again, and then TioN is deposited as a decorative functional layer.
[0081] see image 3 Shown: the first column is equipped with 3 Ti targets, the second column is equipped with 3 AlTi (50 / 50) targets, the third column is equipped with 3 pure metal Al targets, and the fourth column is equipped with 3 AlCr (30 / 50) targets 70); In this embodiment, the arc sources in the 2nd, 3rd and 4th rows are applied with pulsed arc power.
[0082] Referring to table 2, the main process parameters of the present embodiment are as follows:
[0083] 1. Draw a vacuum, heat to 450°C, and set the speed to 2 revolutions / min
[0084] 2. Turn the baffle to the front of the Ti target, pump in argon gas 300 an...
PUM
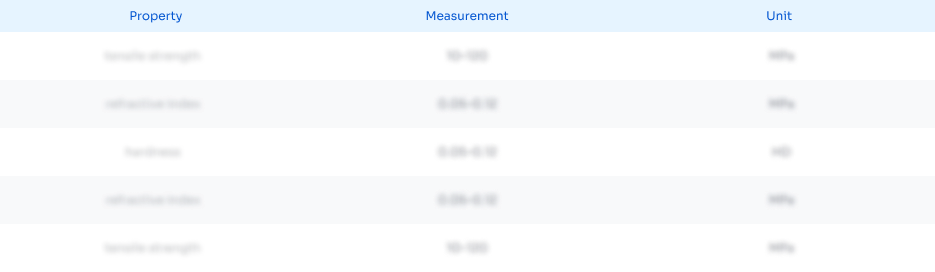
Abstract
Description
Claims
Application Information

- R&D
- Intellectual Property
- Life Sciences
- Materials
- Tech Scout
- Unparalleled Data Quality
- Higher Quality Content
- 60% Fewer Hallucinations
Browse by: Latest US Patents, China's latest patents, Technical Efficacy Thesaurus, Application Domain, Technology Topic, Popular Technical Reports.
© 2025 PatSnap. All rights reserved.Legal|Privacy policy|Modern Slavery Act Transparency Statement|Sitemap|About US| Contact US: help@patsnap.com