Preparation method of PVC resin special for chlorination
A PVC resin and particle technology, applied in the field of polymer materials, can solve the problems of complex process and high risk, and achieve the effects of simple and easy process, high oil absorption rate of plasticizer and large specific surface area
- Summary
- Abstract
- Description
- Claims
- Application Information
AI Technical Summary
Problems solved by technology
Method used
Examples
Embodiment 1
[0023] A preparation method of special PVC resin for chlorination, comprising the following steps:
[0024] Step 1. Weigh 100g of SG-8 PVC resin wet material with a water content of 5% after centrifugation in the water-phase polymerization PVC production system, and place it in a closed container with a stirring device; add 0.5g of methanol to the container at 5°C Stir for 1 minute, and the stirring speed is 50 rpm to obtain the initial material;
[0025] Step 2. Put the homogeneously mixed primary material in step 1 into a microwave reactor for heating. The microwave power is 900w, and the heating time is 1 minute. Rapidly increasing, compressing the structure around the PVC resin particles close together at the initial stage, breaking through the shackles of the outer film of the PVC particles in the later stage, and quickly escaping, so that the internal pore size of the PVC particles increases again, and a large number of holes are formed after the water vapor escapes, whi...
Embodiment 2
[0028] A preparation method of special PVC resin for chlorination, comprising the following steps:
[0029] Step 1, take by weighing 100g of the SG-5 type PVC resin wet material with a water content of 25% after centrifugation in the PVC production system of the aqueous phase polymerization method, and place it in a closed container with a stirring device; add 1.5g of ethanol to the container, and Stir at 35°C for 30 minutes at a stirring speed of 500 rpm to obtain the initial material;
[0030] Step 2. Put the uniformly mixed primary material in step 1 into a microwave reactor for heating. The microwave power is 2000w, and the heating time is 10 minutes. Rapidly increasing, compressing the structure around the PVC resin particles close together at the initial stage, breaking through the shackles of the outer film of the PVC particles in the later stage, and quickly escaping, so that the internal pore size of the PVC particles increases again, and a large number of holes are f...
Embodiment 3
[0033] A preparation method of special PVC resin for chlorination, comprising the following steps:
[0034] Step 1. Weigh 100g of SG-5 PVC resin wet material with a water content of 15% after centrifugation in the PVC polymerization production system, and place it in a closed container with a stirring device; add 1.0g of the weight of the PVC resin wet material to the container Acetone was stirred at 25°C for 10 minutes at a stirring speed of 100 rpm to obtain the initial material;
[0035] Step 2. Put the homogeneously mixed primary material in step 1 into a microwave reactor for heating. The microwave power is 1200w, and the heating time is 5 minutes. Rapidly increasing, compressing the structure around the PVC resin particles close together at the initial stage, breaking through the shackles of the outer film of the PVC particles in the later stage, and quickly escaping, so that the internal pore size of the PVC particles increases again, and a large number of holes are for...
PUM
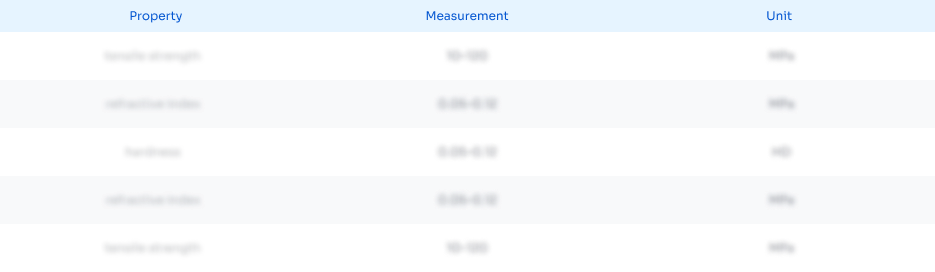
Abstract
Description
Claims
Application Information

- R&D
- Intellectual Property
- Life Sciences
- Materials
- Tech Scout
- Unparalleled Data Quality
- Higher Quality Content
- 60% Fewer Hallucinations
Browse by: Latest US Patents, China's latest patents, Technical Efficacy Thesaurus, Application Domain, Technology Topic, Popular Technical Reports.
© 2025 PatSnap. All rights reserved.Legal|Privacy policy|Modern Slavery Act Transparency Statement|Sitemap|About US| Contact US: help@patsnap.com