High-temperature fuel cell bipolar plate anti-oxidation plating layer
A high-temperature fuel cell, anti-oxidation technology, applied in fuel cells, fuel cell components, electrochemical generators, etc., can solve the problem of increasing the contact resistance between the electrode plate and the gas diffusion layer, reducing the conductivity of the proton exchange membrane, reducing the Fuel cell output performance and other issues, to solve the effect of weak bonding, strong anti-vibration ability, and reduced contact resistance value
- Summary
- Abstract
- Description
- Claims
- Application Information
AI Technical Summary
Problems solved by technology
Method used
Examples
Embodiment 1
[0029] An embodiment of the present invention provides an anti-oxidation coating for a bipolar plate of a high-temperature fuel cell. The anti-oxidation coating for a bipolar plate includes a composite coating, and the composite coating is composed of a CrN film, a silver coating, and a gold coating;
[0030] Wherein, the preparation method of the anti-oxidation coating comprises the following steps:
[0031] 1) Select the stainless steel plate as the bipolar plate material, and pretreat the stainless steel plate, as follows:
[0032] i) First mix the detergent with water and put it into the stainless steel plate, soak it for 30-60 minutes, then scrub it with a sponge ball for 2-3 times, and then rinse it with deionized water; then put the stainless steel plate in 20-30% of the Soak in hydrochloric acid solution for 30-40min, then scrub with steel wool 2-3 times, then rinse with deionized water;
[0033] ii) The stainless steel plate after the above treatment is polished and ...
Embodiment 2
[0040]An embodiment of the present invention provides an anti-oxidation coating for a bipolar plate of a high-temperature fuel cell. The anti-oxidation coating for a bipolar plate includes a composite coating, and the composite coating is composed of a CrN film, a silver coating, and a gold coating;
[0041] Wherein, the preparation method of the anti-oxidation coating comprises the following steps:
[0042] 1) Select the stainless steel plate as the bipolar plate material, and pretreat the stainless steel plate, as follows:
[0043] i) First mix the detergent with water and put it into the stainless steel plate, soak it for 30-60 minutes, then scrub it with a sponge ball for 2-3 times, and then rinse it with deionized water; then put the stainless steel plate in 20-30% of the Soak in hydrochloric acid solution for 30-40min, then scrub with steel wool 2-3 times, then rinse with deionized water;
[0044] ii) The stainless steel plate after the above treatment is polished and p...
Embodiment 3
[0050] An embodiment of the present invention provides an anti-oxidation coating for a bipolar plate of a high-temperature fuel cell. The anti-oxidation coating for a bipolar plate includes a composite coating, and the composite coating is composed of a CrN film, a silver coating, and a gold coating;
[0051] Wherein, the preparation method of the anti-oxidation coating comprises the following steps:
[0052] 1) Select the stainless steel plate as the bipolar plate material, and pretreat the stainless steel plate, as follows:
[0053] i) First mix the detergent with water and put it into the stainless steel plate, soak it for 30-60 minutes, then scrub it with a sponge ball for 2-3 times, and then rinse it with deionized water; then put the stainless steel plate in 20-30% of the Soak in hydrochloric acid solution for 30-40min, then scrub with steel wool 2-3 times, then rinse with deionized water;
[0054] ii) The stainless steel plate after the above treatment is polished and ...
PUM
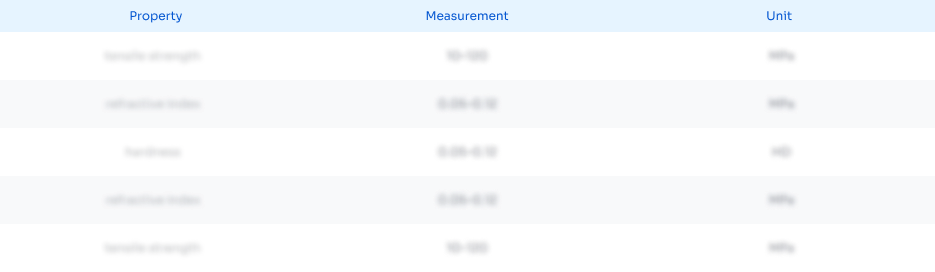
Abstract
Description
Claims
Application Information

- R&D
- Intellectual Property
- Life Sciences
- Materials
- Tech Scout
- Unparalleled Data Quality
- Higher Quality Content
- 60% Fewer Hallucinations
Browse by: Latest US Patents, China's latest patents, Technical Efficacy Thesaurus, Application Domain, Technology Topic, Popular Technical Reports.
© 2025 PatSnap. All rights reserved.Legal|Privacy policy|Modern Slavery Act Transparency Statement|Sitemap|About US| Contact US: help@patsnap.com