Thinning method of lithium niobate wafer
A lithium niobate wafer technology, applied in the thinning field of lithium niobate wafers, can solve the problems of easy brittle failure, low hardness of lithium niobate processing thickness, deep subsurface damage layer, etc., to improve reliability , reduce the risk of fragmentation, and improve the quality of the effect
- Summary
- Abstract
- Description
- Claims
- Application Information
AI Technical Summary
Problems solved by technology
Method used
Image
Examples
Embodiment
[0036] DBG (Dicing Before Grinding) is a commonly used process for wafer backside thinning and cutting. The cutting before grinding process is to reverse the original process of Dicing After Grinding (Dicing After Grinding). That is, the wafer is first half-cut, and then the wafer is divided into chips by back grinding. By using this technology, it is possible to minimize backside cracking and wafer breakage when the chips are divided, so that chips can be smoothly diced from large-sized wafers. Since the chipping phenomenon of the backside of the wafer is greatly reduced, it is possible to perform ultra-thin processing on the wafer while maintaining high flexural strength, so that a high-strength chip can be produced. In addition, since the chips are separated by the grinding process of the grinder, the risk of breakage of thin wafers during transportation can be effectively avoided. The pre-grinding dicing process can minimize the backside cracking caused by the dicing proc...
PUM
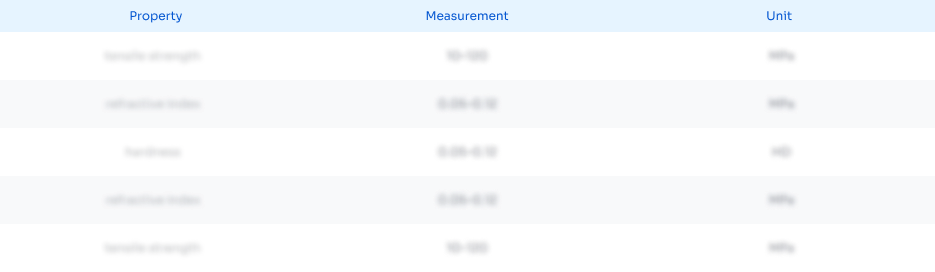
Abstract
Description
Claims
Application Information

- R&D
- Intellectual Property
- Life Sciences
- Materials
- Tech Scout
- Unparalleled Data Quality
- Higher Quality Content
- 60% Fewer Hallucinations
Browse by: Latest US Patents, China's latest patents, Technical Efficacy Thesaurus, Application Domain, Technology Topic, Popular Technical Reports.
© 2025 PatSnap. All rights reserved.Legal|Privacy policy|Modern Slavery Act Transparency Statement|Sitemap|About US| Contact US: help@patsnap.com