A curved surface gradient ceramic part and its manufacturing method
A technology of ceramic parts and manufacturing methods, which is applied in the field of curved surface gradient ceramic parts and its manufacturing, can solve the problems that plane slice additive manufacturing technology is difficult to realize, and achieve the effect of broad application prospects
- Summary
- Abstract
- Description
- Claims
- Application Information
AI Technical Summary
Problems solved by technology
Method used
Image
Examples
Embodiment 1
[0038] The method of manufacturing the surface gradient ceramic parts provided in Example 1 of the present invention mainly includes the following steps:
[0039] Step (a): The acrylic resin, 2,2-dimethoxy-2-phenylceneethylenethylideophenone, polyacrylate is uniformly mixed, wherein the quality of the photoinitiator is a photosensitive resin mass. 1 wt%, the mass of the dispersant is 2 wt% of the mass of ceramic powder. Next, weigh the appropriate amount of Al 2 O 3 Zro 2 Ceramic powder, adjust the ratio of each component, and then mixed the ceramic powder and the photosensitive premixing mixed with gas in the planetary ball mill, and finally obtained Al 2 O 3 Ceramic powder in ceramic paste accounts for 40 vol%, photosensitive premix 60 vol%; Zro 2 Ceramic powder in ceramic paste accounts for 60 vol%, and 40 vol% of the photosensitive premix.
[0040] Step (b): The computer assist software is used to design a surface characteristic of the surface characteristics, and the modeling...
Embodiment 2
[0044] The method of manufacturing the surface gradient ceramic parts provided in Example 2 of the present invention mainly includes the steps of:
[0045] Step (a): Mix the acrylic resin, 1-hydroxycyclohexylphenyl ketone, and sodium polyacrylate to be uniformly mixed, wherein the quality of the photoinitiator is 2 wt% of the photosensitive resin mass, the mass of the dispersant. It is 3 wt% of the mass of ceramic powder. Next, weigh the appropriate amount of Al 2 O 3 Zro 2 Ceramic powder, adjust the ratio of each component, and then mixed the ceramic powder and the photosensitive premixing mixed with gas in the planetary ball mill, and finally obtained Al 2 O 3 Ceramic powder in ceramic paste accounts for 50 vol%, 50 vol% of photosensitive premix; Al 2 O 3 / Zro 2 Composite ceramic paste in Al 2 O 3 Zro 2 Ceramic powder accounted for 50 vol%, 50 vol% of the photosensitive premix.
[0046] Step (b): Designing the surface characteristics of the surface characteristics by computer a...
Embodiment 3
[0050] The method of manufacturing surface gradient ceramic parts provided in Example 3 of the present invention mainly includes the following steps:
[0051] Step (a): Ephenyl phosphine, 2,4,6-trimethylbenzoyl-diphenyl oxide, tetramethylammonium hydroxide, is uniformly mixed, wherein the photoinitiator The mass is 3% by weight of the mass of the photosensitive resin, the mass of the dispersant is 4 wt% of the mass of ceramic powder. Next, weigh the appropriate amount of Si 3 N 4 The ceramic powder, adjusts the ratio of each component, and then mixed the ceramic powder and the photosensitive pre-mixture in the planetary ball mill, and finally obtaining a component Si. 3 N 4 Ceramic powder in ceramic paste accounts for 60 vol%, photosensitive premix 40 vol%; B component Si 3 N 4 Ceramic powder in ceramic paste accounted for 40 vol%, photosensitive premix 60 vol%.
[0052] Step (b): The use of computer assist software to design a surface gradient ceramic parts model with surface fea...
PUM
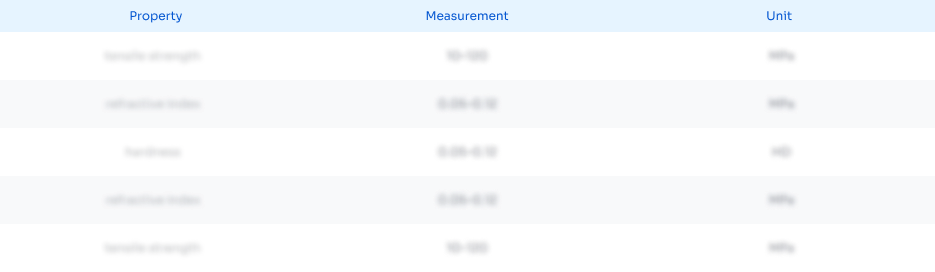
Abstract
Description
Claims
Application Information

- Generate Ideas
- Intellectual Property
- Life Sciences
- Materials
- Tech Scout
- Unparalleled Data Quality
- Higher Quality Content
- 60% Fewer Hallucinations
Browse by: Latest US Patents, China's latest patents, Technical Efficacy Thesaurus, Application Domain, Technology Topic, Popular Technical Reports.
© 2025 PatSnap. All rights reserved.Legal|Privacy policy|Modern Slavery Act Transparency Statement|Sitemap|About US| Contact US: help@patsnap.com