Underwater local dry laser welding system and welding method thereof
A technology of laser welding and partial dry method, which is applied in the direction of laser welding equipment, welding equipment, mechanical equipment, etc., can solve the problems of difficulty in obtaining welding status, unfavorable welding quality, and insufficient self-monitoring ability, so as to improve the stability of driving current and response speed, improve welding accuracy and welding quality, and realize the effects of real-time monitoring and fine control
- Summary
- Abstract
- Description
- Claims
- Application Information
AI Technical Summary
Problems solved by technology
Method used
Image
Examples
Embodiment
[0036] This embodiment is an underwater partial dry laser welding system, its structure is as follows figure 1 As shown, including industrial computer, underwater robot, SiC laser welding power supply, laser welding head, micro drainage device, drainage gas device, shielding gas device, water cooling device, endoscope and panoramic camera; the output end of SiC laser welding power supply through The optical fiber is connected to the laser welding head; the panoramic camera, the laser welding head and the micro-drainage device are respectively set on the underwater robot; the laser welding head is located in the micro-drainage device and connected to the shielding gas device; In the cavity, to obtain the internal image of the welding cavity; the drainage gas device communicates with the welding cavity of the micro drainage device; the underwater robot, SiC laser welding power supply, drainage gas device, protective gas device, water cooling device, endoscope and The panoramic c...
PUM
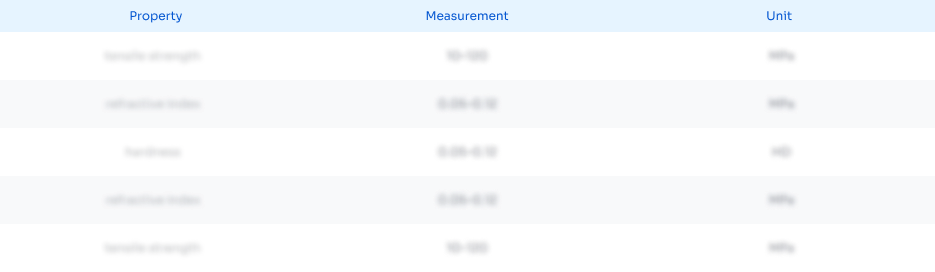
Abstract
Description
Claims
Application Information

- R&D Engineer
- R&D Manager
- IP Professional
- Industry Leading Data Capabilities
- Powerful AI technology
- Patent DNA Extraction
Browse by: Latest US Patents, China's latest patents, Technical Efficacy Thesaurus, Application Domain, Technology Topic, Popular Technical Reports.
© 2024 PatSnap. All rights reserved.Legal|Privacy policy|Modern Slavery Act Transparency Statement|Sitemap|About US| Contact US: help@patsnap.com