Method for recovering molybdenum from low-molybdenum ammonia leaching residues
A technology for ammonia leaching and molybdenum slag, applied in the field of molybdenum recovery, can solve the problems of complicated procedures, low economic benefit and high cost, and achieve the effects of environmental protection of the process flow, simple and easy process, and low production cost.
- Summary
- Abstract
- Description
- Claims
- Application Information
AI Technical Summary
Problems solved by technology
Method used
Image
Examples
Embodiment 1
[0050] The ammonia leaching slag of an associated molybdenum ore smelting and processing enterprise has the following components:
[0051]
[0052] (1) dehydrating the low-molybdenum ammonia leaching slag after ammonia leaching, 300g of ammonia leaching slag after water, water content 20.15%;
[0053] (2) Add low-molybdenum ammonia leaching slag to 90g of sodium carbonate and water for stirring and slurrying, and the liquid-solid ratio is 3:1;
[0054] (3) Seal and heat the reactor to 95°C to 100°C, pressurize and feed oxygen to a pressure of 0.5Mpa;
[0055] (4) Heating to 180°C for reaction;
[0056] (5) Stir at constant temperature, pressurize and react for 2 hours;
[0057] (6) Repeat the above steps to carry out three groups of tests and the results are as follows:
[0058]
Embodiment 2
[0060] The ammonia leaching slag after three times ammonia leaching in an associated molybdenum ore smelting and processing enterprise has the following components:
[0061]
[0062] Carry out extended line test, parallel test 3 groups, each group ammonia leaching slag weight 5Kg.
[0063] (1) Dehydrate the low-molybdenum ammonia leaching slag after ammonia leaching, 5Kg of ammonia leaching slag after water, water content 22.05%;
[0064] (2) Add the low-molybdenum ammonia leaching slag to 1.2Kg of sodium carbonate and water for stirring and slurrying, and the liquid-solid ratio is 2:1;
[0065] (3) Seal and heat the reactor to 95°C to 100°C, pressurize and feed oxygen to a pressure of 0.5Mpa;
[0066] (4) Heating to 180°C for reaction;
[0067] (5) Stir at constant temperature, pressurize and react for 2 hours;
[0068] (6) Repeat the above steps to carry out three groups of tests and the results are as follows:
[0069]
PUM
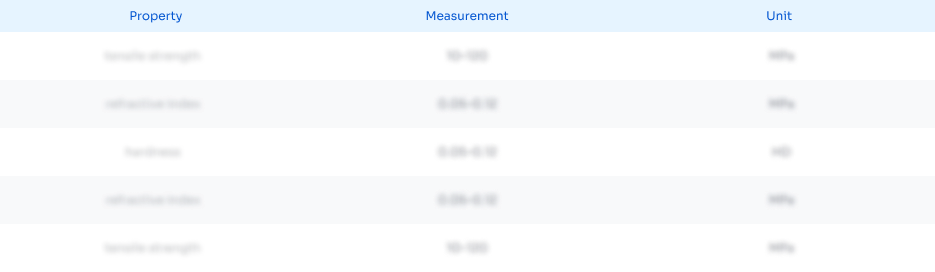
Abstract
Description
Claims
Application Information

- R&D Engineer
- R&D Manager
- IP Professional
- Industry Leading Data Capabilities
- Powerful AI technology
- Patent DNA Extraction
Browse by: Latest US Patents, China's latest patents, Technical Efficacy Thesaurus, Application Domain, Technology Topic, Popular Technical Reports.
© 2024 PatSnap. All rights reserved.Legal|Privacy policy|Modern Slavery Act Transparency Statement|Sitemap|About US| Contact US: help@patsnap.com