Hydrofining catalyst and preparation method thereof
A technology for hydrorefining and catalysts, which is applied in catalyst activation/preparation, chemical instruments and methods, physical/chemical process catalysts, etc., and can solve problems affecting catalyst performance, active metal agglomeration, etc.
- Summary
- Abstract
- Description
- Claims
- Application Information
AI Technical Summary
Problems solved by technology
Method used
Examples
Embodiment 1
[0038] Nickel nitrate was added into the dissolving tank 1 equipped with deionized water to prepare mixed solution A, and the weight concentration of Ni in mixed solution A was 55g / L in terms of NiO. Nickel nitrate is equipped with the dissolving tank 2 of deionized water, is mixed with mixed solution B, and the weight concentration of Ni in NiO in solution B is 40g / L. Deionized water is added in the reaction tank, and the weight concentration is based on Al 2 o 3 30g / L sodium metaaluminate solution and mixed solution A are added into the reaction tank in parallel flow for gelation reaction, the gelation temperature is kept at 55°C, the pH value is controlled at 7.6 during the co-flow gelation reaction process, and the gelation time Controlled at 0.8 hour, generate slurry I. The obtained precipitate slurry I was aged under stirring, the stirring speed was 200 rpm, the aging temperature was 75° C., the aging pH value was controlled at 7.2, and the aging was 0.7 hours. After ...
Embodiment 2
[0040] According to the method of Example 1, according to the component content ratio of catalyst B in Table 1, nickel nitrate and ammonium metatungstate are added to the dissolution tank 1 to prepare mixed solution A, and the weight concentration of Ni in mixed solution A is calculated as NiO 20.6g / L, W is WO 3 The weight concentration of meter is 20g / L. Add nickel nitrate to the dissolving tank 2 to prepare mixed solution B, the weight concentration of Ni in mixed solution B is 32g / L in terms of NiO. Add deionized water in the reaction tank, the weight concentration is based on Al 2 o 3 Add 22g / L sodium metaaluminate solution and mixed solution A into the reaction tank in parallel flow, keep the gelling temperature at 50°C, control the pH value at 7.4 during the co-flow gelling reaction process, and control the gelling time at 1.1 hours , generating slurry I. The obtained precipitate slurry I was aged under stirring, the stirring speed was 180 rpm, the aging temperature ...
Embodiment 3
[0042] According to the composition ratio of the catalyst C in Table 1, ammonium metatungstate is added to the dissolution tank 1 to prepare a mixed solution A, and W in the mixed solution A is made of WO 3 The weight concentration of meter is 34g / L. Add ammonium metatungstate to the dissolving tank 2 to prepare mixed solution B, W in mixed solution B is WO 3 The weight concentration of the meter is 20g / L. Add deionized water in the reaction tank, the weight concentration is based on Al 2 o 3 28g / L sodium metaaluminate solution and mixed solution A are added into the reaction tank in parallel flow, the gelling temperature is kept at 60°C, the pH value is controlled at 7.1 during the co-current gelling reaction process, and the gelling time is controlled at 1.2 hours , generating slurry I. The obtained precipitate slurry I was aged under stirring, the stirring speed was 190 rpm, the aging temperature was 72° C., the aging pH value was controlled at 6.8, and the aging was 0....
PUM
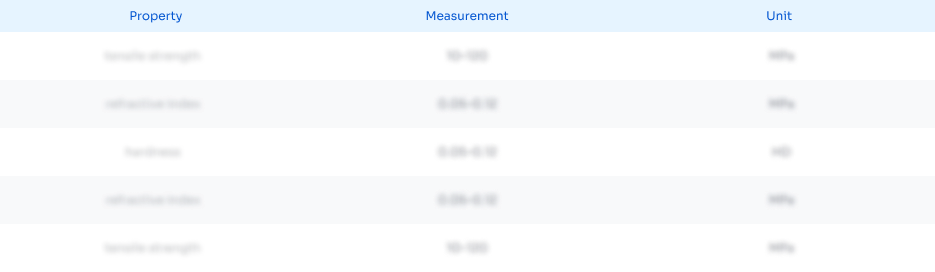
Abstract
Description
Claims
Application Information

- R&D
- Intellectual Property
- Life Sciences
- Materials
- Tech Scout
- Unparalleled Data Quality
- Higher Quality Content
- 60% Fewer Hallucinations
Browse by: Latest US Patents, China's latest patents, Technical Efficacy Thesaurus, Application Domain, Technology Topic, Popular Technical Reports.
© 2025 PatSnap. All rights reserved.Legal|Privacy policy|Modern Slavery Act Transparency Statement|Sitemap|About US| Contact US: help@patsnap.com