Preparation method of copper-aluminum layered composite material capable of effectively controlling interface reaction
A layered composite material and interface control technology, applied in the direction of metal layered products, chemical instruments and methods, lamination, etc., can solve the problem that the uniformity of product performance is difficult to be guaranteed, affect the thermal conductivity and electrical conductivity of materials, and the rolling and compounding process Complicated problems, to achieve the integrated design of structure and function, improve the combination of interface reactions, and ensure the effect of thermal conductivity and electrical conductivity
- Summary
- Abstract
- Description
- Claims
- Application Information
AI Technical Summary
Problems solved by technology
Method used
Image
Examples
Embodiment 1
[0027] This embodiment includes the following steps:
[0028] Step 1. Place the Al foil with a size of 50mm×50mm×0.1mm (length×width×thickness) in a NaOH solution with a mass concentration of 5% for cleaning for 5 seconds, and dry it after neutralization to complete the surface pretreatment, and then carry out GO / Al foil is obtained by electrophoretic deposition of graphene oxide, and then placed in a vacuum drying oven for drying treatment; the electrophoretic deposition solution used in the electrophoretic deposition contains GO and Al(NO 3 ) 3 C 2 h 5 OH solution, the content of GO in the electrophoretic deposition solution is 0.75g / L, Al(NO 3 ) 3 content of 0.25g / L, the voltage used for electrophoretic deposition is 120V, and the time of electrophoretic deposition is 20s;
[0029] Step 2. Place the Cu foil with a size of 50mm×50mm×0.04mm (length×width×thickness) in an HCl solution with a mass concentration of 5% for cleaning for 5 seconds, and dry it after neutralizat...
Embodiment 2
[0042] This embodiment includes the following steps:
[0043] Step 1. Place the Al foil with a size of 50mm×50mm×0.1mm (length×width×thickness) in a NaOH solution with a mass concentration of 5% for 10 seconds, and then dry it after neutralization to complete the surface pretreatment, and then carry out GO / Al foil is obtained by electrophoretic deposition of graphene oxide, and then placed in a vacuum drying oven for drying treatment; the electrophoretic deposition solution used in the electrophoretic deposition contains GO and Al(NO 3 ) 3 C 2 h 5 OH solution, the content of GO in the electrophoretic deposition solution is 1.25g / L, Al(NO 3 ) 3 The content is 0.5g / L, the voltage used for electrophoretic deposition is 100V, and the electrophoretic deposition time is 60s;
[0044] Step 2: Place the Cu foil with a size of 50mm×50mm×0.1mm (length×width×thickness) in an HCl solution with a mass concentration of 5% for 10 seconds, and then dry it after neutralization treatment t...
Embodiment 3
[0048] This embodiment includes the following steps:
[0049] Step 1. Place the Al foil with a size of 50mm×50mm×0.1mm (length×width×thickness) in a NaOH solution with a mass concentration of 5% for 7 seconds, and then dry it after neutralization treatment to complete the surface pretreatment, and then carry out GO / Al foil is obtained by electrophoretic deposition of graphene oxide, and then placed in a vacuum drying oven for drying treatment; the electrophoretic deposition solution used in the electrophoretic deposition contains GO and Al(NO 3 ) 3 C 2 h 5 OH solution, the content of GO in the electrophoretic deposition solution is 0.5g / L, Al(NO 3 ) 3 content of 0.125g / L, the voltage used for electrophoretic deposition is 150V, and the time of electrophoretic deposition is 10s;
[0050] Step 2. Place the Cu foil with a size of 50mm×50mm×0.04mm (length×width×thickness) in an HCl solution with a mass concentration of 5% for cleaning for 7 seconds, and dry it after neutraliz...
PUM
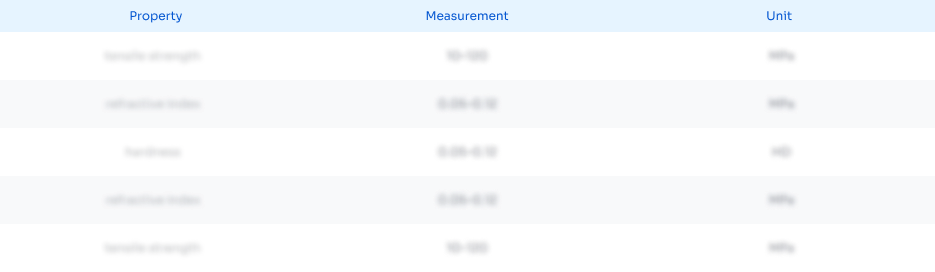
Abstract
Description
Claims
Application Information

- Generate Ideas
- Intellectual Property
- Life Sciences
- Materials
- Tech Scout
- Unparalleled Data Quality
- Higher Quality Content
- 60% Fewer Hallucinations
Browse by: Latest US Patents, China's latest patents, Technical Efficacy Thesaurus, Application Domain, Technology Topic, Popular Technical Reports.
© 2025 PatSnap. All rights reserved.Legal|Privacy policy|Modern Slavery Act Transparency Statement|Sitemap|About US| Contact US: help@patsnap.com