Automatic tool changing system and tool changing method
A technology of automatic tool change and tool change mechanism, which is applied in the field of mechanical processing and can solve problems such as low efficiency
- Summary
- Abstract
- Description
- Claims
- Application Information
AI Technical Summary
Problems solved by technology
Method used
Image
Examples
Embodiment 1
[0031] Such as figure 1 The shown automatic tool change system includes a tool change mechanism and a tool clamping mechanism; the tool change mechanism includes a rotor disk 7 arranged on the motor shaft 3, and an electromagnetic assembly is arranged on the rotor disk 7; the electronic shaft adopts a spline shaft , which can be better suited to the requirements of high-speed rotation during tool processing. The tool clamping mechanism includes a tool disc 10 for clamping tools, and the end surface of the tool disc 10 close to the rotor disc 7 is provided with an armature disc 8 that cooperates with the electromagnetic assembly; The holding mechanism is connected to the tool change mechanism or separated from the tool change mechanism.
[0032] When the electromagnetic component is powered on, it generates magnetic force to attract the armature disc 8, thereby attracting the tool disc 10 and connecting it with the rotor disc 7; when the electromagnetic component is powered of...
Embodiment 2
[0041]The tool change mechanism of the automatic tool change system is usually installed on the robot, and multiple tool disks with tools are installed on the tool holder. By controlling the movement of the robot and the tool change mechanism, the automatic change of the tool can be realized. The specific steps are as follows:
[0042] When it is necessary to change the tool during processing, the robot controls the movement of the tool change mechanism, so that the tool change mechanism can be accurately positioned on the vacancy on the tool holder where the tool disc can be placed, and the electromagnetic coil assembly is controlled to be powered off. Disengage from the tool changing mechanism, and place the tool disc 10 on the tool rest.
[0043] Then the tool changing mechanism is controlled to move to the corresponding position above the tool disc 10 to be replaced; the electromagnetic coil assembly is controlled to be energized, and the tool disc 10 is connected to the to...
PUM
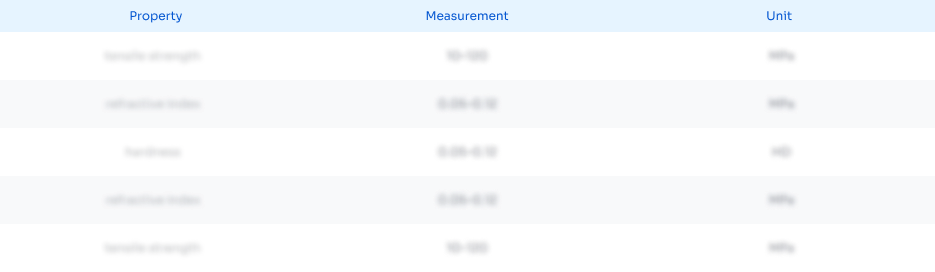
Abstract
Description
Claims
Application Information

- Generate Ideas
- Intellectual Property
- Life Sciences
- Materials
- Tech Scout
- Unparalleled Data Quality
- Higher Quality Content
- 60% Fewer Hallucinations
Browse by: Latest US Patents, China's latest patents, Technical Efficacy Thesaurus, Application Domain, Technology Topic, Popular Technical Reports.
© 2025 PatSnap. All rights reserved.Legal|Privacy policy|Modern Slavery Act Transparency Statement|Sitemap|About US| Contact US: help@patsnap.com