Stone coal vanadium ore oxidation grain breaking roasting comprehensive utilization method
A technology of stone coal vanadium and crystal breaking, applied in the direction of silicon oxide, silicon dioxide, process efficiency improvement, etc., can solve the problems of low heat utilization rate, low processing capacity, high cost, etc., and achieve low operating cost and large processing capacity , energy consumption and low cost effect
- Summary
- Abstract
- Description
- Claims
- Application Information
AI Technical Summary
Problems solved by technology
Method used
Image
Examples
Embodiment 1
[0051] The process is like figure 1 Shown
[0052] Crush the stone coal vanadium ore to a particle size of ≤15mm, and then grind the ore to a particle size of ≤1mm, and the part with a particle size of 0.074mm accounts for 62% of the total mass to obtain fine ore; the stone coal vanadium ore contains SiO by mass percentage 2 58.77%, Al 2 O 3 7.2%, V 2 O 5 1.05%, TFe 2~3%, CaO 3.22%, MgO 1.22%, Na 2 O 1.11%, C 12.5%;
[0053] The powder ore is continuously conveyed to the suspension decarburization roaster through the screw feeder; the bottom of the suspension decarburization furnace is equipped with a first burner and a gas inlet, the top is equipped with a feed inlet, and the upper part is equipped with a discharge outlet and the first cyclone The separator is connected; the gas is fed into the first burner, and oxygen and air are fed into the gas inlet of the suspension decarburization furnace, and the flue gas generated by the combustion of the first burner enters the suspensi...
Embodiment 2
[0062] The method is the same as in Example 1, the difference is:
[0063] (1) The part with a diameter of 0.074mm in the fine ore accounts for 65% of the total mass; the stone coal vanadium ore contains SiO according to the mass percentage 2 60.2%, Al 2 O 3 7.4%, V 2 O 5 1.1%, TFe 2.55%, CaO 2.78%, MgO 1.43%, Na 2 O 1.25%, C11.56%;
[0064] (2) The decarburization reaction temperature is 800℃; the residence time of the fine ore in the suspension decarburization roaster is 40min; the volume flow ratio of oxygen and air is 1:2;
[0065] (3) Crystal breaking oxidation reaction temperature is 850℃; the residence time of the decarburized material in the suspension crystal breaking roaster is 90 minutes; the volume flow ratio of oxygen and air is 1:5;
[0066] (4) The oxide material is discharged when the temperature is reduced to 180℃, and the air temperature after heat exchange is 650℃;
[0067] (5) Mix the cooled oxide material with a sulfuric acid solution with a mass concentration of ...
Embodiment 3
[0072] The method is the same as in Example 1, the difference is:
[0073] (1) The part with a particle size of 0.074mm in the fine ore accounts for 68% of the total mass; the stone coal vanadium ore contains SiO by mass percentage 2 61.43%, Al 2 O 3 7.96%, V 2 O 5 0.74%, TFe 2.97%, CaO 3.38%, MgO 1.28%, Na 2 O0.95%, C10.36%;
[0074] (2) The decarburization reaction temperature is 850℃; the residence time of the fine ore in the suspension decarburization roaster is 30min; the volumetric flow ratio of oxygen and air is 1:3;
[0075] (3) Crystal breaking oxidation reaction temperature is 900℃; the residence time of the decarburized material in the suspension crystal breaking roaster is 60min; the volume flow ratio of oxygen and air is 1:8;
[0076] (4) The oxide material is discharged when the temperature is lowered to 200℃, and the air temperature after heat exchange is 700℃;
[0077] (5) The mass concentration of the sulfuric acid solution is 85%; the mass of the sulfuric acid soluti...
PUM
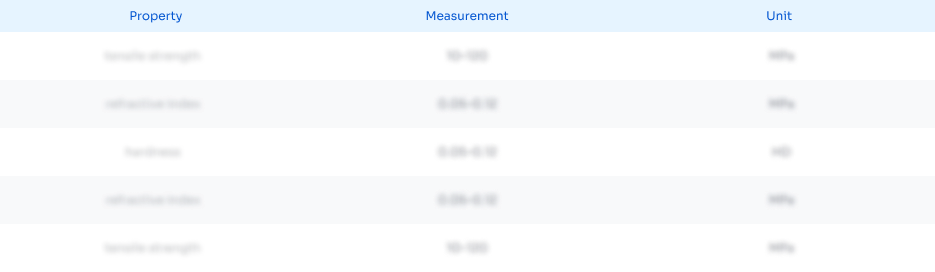
Abstract
Description
Claims
Application Information

- R&D
- Intellectual Property
- Life Sciences
- Materials
- Tech Scout
- Unparalleled Data Quality
- Higher Quality Content
- 60% Fewer Hallucinations
Browse by: Latest US Patents, China's latest patents, Technical Efficacy Thesaurus, Application Domain, Technology Topic, Popular Technical Reports.
© 2025 PatSnap. All rights reserved.Legal|Privacy policy|Modern Slavery Act Transparency Statement|Sitemap|About US| Contact US: help@patsnap.com