A method and device for denitrification and heat recovery of industrial furnace flue gas
A heat recovery and industrial furnace technology, applied in chemical instruments and methods, separation methods, combustion methods, etc., can solve the problems of pressure pollutant content fluctuations, system paralysis, low valve synchronization, etc., to achieve strong adaptability to load changes, The effect of solving thiamine blockage
- Summary
- Abstract
- Description
- Claims
- Application Information
AI Technical Summary
Problems solved by technology
Method used
Image
Examples
Embodiment 1
[0095] A hydrocarbon-containing tail gas incinerator, the flue gas temperature after incineration is 1250℃, the flue gas basically does not contain SOx, and the NOx content is 400mg / m 3 n. The nitrogen oxide content in the outlet flue gas is monitored online by the online monitoring instrument (CEMS) 93, and the air volume of the blower 95 is adjusted so that the hydrocarbons in the combustion furnace are not completely burned, and trace amounts of CO and H are generated. 2 . Regenerative reaction - in heat exchange module 1, CO and H 2 Reacts with NOx in the U-shaped regenerator 20, and the reaction regenerator 21 uses mullite as the base material, and the surface is impregnated with V 2 O 5 / MnO 3 / WO 3 Active metal compound components. The reversing valve 10 is switched every 3 minutes. After treatment, the temperature of the exhaust flue gas is reduced to 150°C, and the NOx in the flue gas is reduced to 80mg / m 3 n, which meets the emission index requirements, and is...
Embodiment 2
[0097] An incomplete regeneration reactor, the outlet flue gas temperature is 700 °C, and the SOx content is 800 mg / m 3 n, NOx content 200mg / m 3 n, CO content 1000mg / m 3 n. Since there is no combustion furnace, there is no process of online adjustment of the air volume, the flue gas directly enters the regenerative reaction-heat exchange assembly 1, CO reacts with NOx in the U-shaped regenerator 20, and the reaction regenerator 21 reacts with NOx. Based on honeycomb ceramic, impregnated with CeO 2 / La 2 O 3Active metal catalyst component. The reversing valve 10 is switched every 2 minutes, and the heat of the regenerator is used to heat the process gas with a fixed flow rate, which saves the steam consumption originally used for heating the process gas. Regenerative reaction - the flue gas temperature at the outlet of heat exchange component 1 drops to 100°C, the SOx content is slightly reduced, and the NOx content is reduced to 65mg / m 3 n, CO content reduced to 840mg / m...
Embodiment 3
[0099] A VOCs treatment facility uses RCO to treat VOCs. The temperature of the exhaust gas produced is 450°C and the SOx content is 30mg / m2 3 n, NOx content 120mg / m 3 n, CO content 250mg / m 3 n. The exhaust gas directly enters the regenerative reaction-heat exchange assembly 1, CO reacts with NOx in the U-shaped regenerator 20, and the reaction regenerator 21 is made of a steel plate base material, inlaid with Zn α / HKUST zinc-copper bimetallic organocatalyst. The reversing valve 10 is switched every 2 minutes. After treatment, the temperature of the exhaust flue gas is reduced to 120°C, and the NOx in the flue gas is reduced to 70mg / m 3 n, CO content 170mg / m 3 n Meet the emission target requirements. The heat of the regenerator is used to heat the air for RCO oxidation at a fixed flow rate, which saves the fuel consumption of the RCO device.
PUM
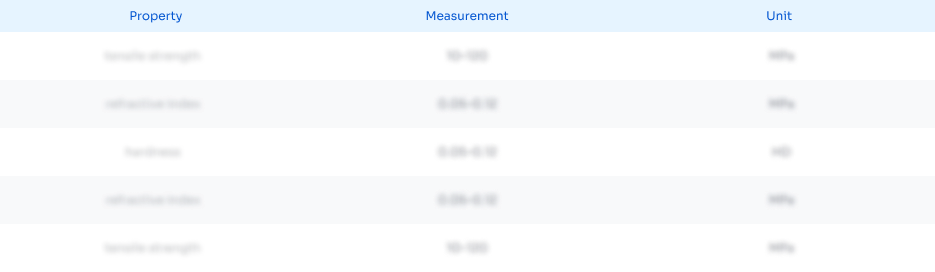
Abstract
Description
Claims
Application Information

- R&D
- Intellectual Property
- Life Sciences
- Materials
- Tech Scout
- Unparalleled Data Quality
- Higher Quality Content
- 60% Fewer Hallucinations
Browse by: Latest US Patents, China's latest patents, Technical Efficacy Thesaurus, Application Domain, Technology Topic, Popular Technical Reports.
© 2025 PatSnap. All rights reserved.Legal|Privacy policy|Modern Slavery Act Transparency Statement|Sitemap|About US| Contact US: help@patsnap.com