Method for upgrading coal pyrolysis
A technology of coal pyrolysis and pyrolyzer, which is applied in direct heating dry distillation, gas dedusting, petroleum industry, etc. It can solve the problems of low tar quality, low heat utilization rate, poor pyrolysis dedusting effect, etc., and achieve high dedusting efficiency, Simplify operation and solve the effect of tar dust clogging
- Summary
- Abstract
- Description
- Claims
- Application Information
AI Technical Summary
Problems solved by technology
Method used
Image
Examples
Embodiment 1
[0050] Baorixile lignite with a particle size of ≤30mm (see Table 1 for coal quality analysis data) is continuously fed into the rotary dryer at a rate of 1.5t / h, and flows through the rotary dryer in parallel with hot flue gas at a temperature of about 460°C. During this process, the lignite and the hot flue gas exchange heat directly, and the moisture contained in the lignite is removed as much as possible. In the rotary dryer, the lignite raw material and the hot semi-coke from the pyrolyzer are subjected to indirect heat exchange at the same time, the raw coal and the hot flue gas flow through the inner sleeve, and the hot semi-coke flows through the inner sleeve and the inner sleeve of the rotary dryer. The annular space formed between the outer cylinders. Finally, the lignite is heated to about 130°C, the moisture in the lignite is reduced to about 4%, and the hot semi-coke is cooled to about 180°C.
[0051] The dried lignite at about 130°C and the hot semi-coke at abou...
Embodiment 2
[0058] Raw material coal that present embodiment adopts, test device are identical with embodiment 1, and main operation step is also substantially identical with embodiment 1, and main difference is as follows:
[0059] The lignite is continuously fed into the rotary dryer at a rate of 1.5t / h, and is exchanged with hot flue gas at a temperature of 440°C for dehydration. Finally, the lignite is heated to 110°C, its moisture is reduced to about 6%, and the semi-coke product is cooled to Around 220°C.
[0060] The dried lignite and the hot semi-coke at about 750°C from the heating rotary kiln are mixed with a screw mixer at a weight ratio of 1:6 and then sent to the moving bed pyrolyzer. The lignite raw material and the high-temperature semi-coke are directly exchanged and Pyrolysis occurs to generate hot semi-coke and gas containing tar vapor, and the final pyrolysis temperature is about 650°C.
[0061] The gas containing tar vapor generated in the moving bed pyrolyzer is sent...
PUM
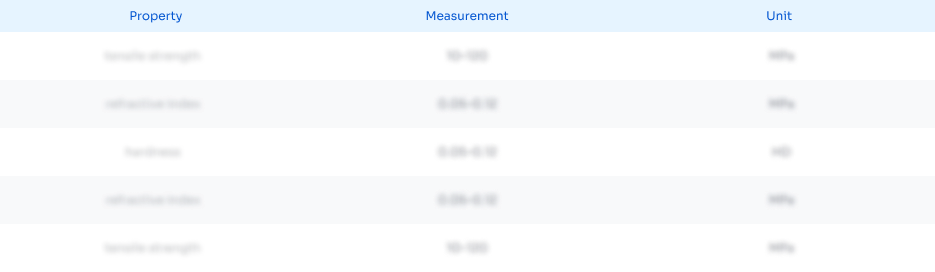
Abstract
Description
Claims
Application Information

- R&D
- Intellectual Property
- Life Sciences
- Materials
- Tech Scout
- Unparalleled Data Quality
- Higher Quality Content
- 60% Fewer Hallucinations
Browse by: Latest US Patents, China's latest patents, Technical Efficacy Thesaurus, Application Domain, Technology Topic, Popular Technical Reports.
© 2025 PatSnap. All rights reserved.Legal|Privacy policy|Modern Slavery Act Transparency Statement|Sitemap|About US| Contact US: help@patsnap.com