Preparation method of high-strength thermal insulation mortar
一种保温砂浆、高强度的技术,应用在陶瓷制品、应用、家里用具等方向,能够解决导热系数、干表观密度和收缩率大、搅拌工艺不合理搅拌时间搅拌强度、不能满足保温砂浆特殊要求等问题,达到缩短固化干燥的时间、降低干表观密度、导热系数降低的效果
- Summary
- Abstract
- Description
- Claims
- Application Information
AI Technical Summary
Problems solved by technology
Method used
Image
Examples
Embodiment 1
[0025] A thermal insulation mortar, in parts by weight, comprising the following raw materials: 112 parts of Portland cement, 8 parts of fly ash, 10 parts of limestone powder, 14 parts of polystyrene particles, 10 parts of bentonite, 4 parts of thickener, 6 parts of double fly powder, 5 parts of thickener, 3 parts of carboxyethyl methylcellulose, 1.2 parts of sodium lauryl sulfate, 13 parts of calcium fluoride, 15 parts of styrene-maleic anhydride copolymer, 26 parts of sodium carbonate , 6 parts of hydrochloric acid.
[0026] The thickener is cellulose ether;
[0027] Described tackifier is ethylene-vinyl acetate copolymer latex powder;
[0028] The molar concentration of described hydrochloric acid is 3mol / L;
[0029] The preparation method of described thermal insulation mortar, comprises the following steps:
[0030] S1: Mix Portland cement, fly ash, limestone powder, polystyrene granules, bentonite, thickener, double fly powder, thickener, carboxyethyl methyl cellulose...
Embodiment 2
[0034] A kind of thermal insulation mortar, which comprises the following raw materials in parts by weight: 96 parts of Portland cement, 5 parts of fly ash, 12 parts of limestone powder, 15 parts of polystyrene particles, 9 parts of bentonite, 5 parts of thickener, 4 parts of double fly powder, 6 parts of thickening agent, 2 parts of carboxyethyl methyl cellulose, 0.8 parts of sodium lauryl sulfate, 14 parts of calcium fluoride, 16 parts of silicone-polyurethane copolymer, 22 parts of sodium carbonate, 7 parts of hydrochloric acid.
[0035] The thickener is cellulose ether;
[0036] Described tackifier is ethylene-vinyl acetate copolymer latex powder;
[0037] The molar concentration of described hydrochloric acid is 2mol / L;
[0038] The preparation method of described thermal insulation mortar, comprises the following steps:
[0039] S1: Mix Portland cement, fly ash, limestone powder, polystyrene granules, bentonite, thickener, double fly powder, thickener, carboxyethyl meth...
Embodiment 3
[0043] A thermal insulation mortar, in parts by weight, comprising the following raw materials: 120 parts of Portland cement, 10 parts of fly ash, 6 parts of limestone powder, 10 parts of polystyrene particles, 12 parts of bentonite, 3 parts of thickener, 7 parts of double fly powder, 4 parts of thickener, 4 parts of carboxyethyl methylcellulose, 1.5 parts of sodium lauryl sulfate, 12 parts of calcium fluoride, styrene maleic anhydride copolymer or silicone-polyurethane copolymer 10 parts, 28 parts of sodium carbonate, 8 parts of hydrochloric acid.
[0044] The thickener is cellulose ether;
[0045] Described tackifier is ethylene-vinyl acetate copolymer latex powder;
[0046] The molar concentration of described hydrochloric acid is 4mol / L;
[0047] The preparation method of described thermal insulation mortar, comprises the following steps:
[0048] S1: Mix Portland cement, fly ash, limestone powder, polystyrene granules, bentonite, thickener, double fly powder, thickener...
PUM
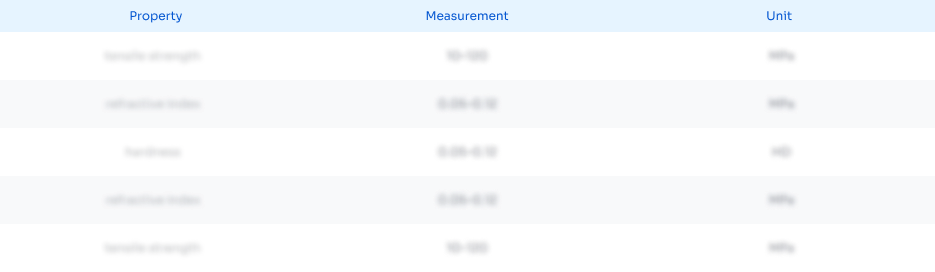
Abstract
Description
Claims
Application Information

- R&D Engineer
- R&D Manager
- IP Professional
- Industry Leading Data Capabilities
- Powerful AI technology
- Patent DNA Extraction
Browse by: Latest US Patents, China's latest patents, Technical Efficacy Thesaurus, Application Domain, Technology Topic, Popular Technical Reports.
© 2024 PatSnap. All rights reserved.Legal|Privacy policy|Modern Slavery Act Transparency Statement|Sitemap|About US| Contact US: help@patsnap.com