10CrNi3MoV round tube blank and preparation method and application thereof
A round tube billet and forging technology, which is applied in the field of 10CrNi3MoV round tube billet and its preparation, can solve the problems of welding seam welding quality risk, short service life of equipment structure, and weld seam is easy to be corroded, so as to improve the density and purity , good toughness, and the effect of reducing component segregation
- Summary
- Abstract
- Description
- Claims
- Application Information
AI Technical Summary
Problems solved by technology
Method used
Image
Examples
preparation example Construction
[0024] The first aspect of the present invention provides a kind of preparation method of 10CrNi3MoV round tube billet, and this method comprises the following steps:
[0025] (1) Carry out batching according to formula quantity, after carrying out electric arc furnace smelting, ladle furnace refining, vacuum degassing refining successively, obtain electroslag consumable electrode;
[0026] (2) performing electroslag remelting on the electroslag consumable electrode obtained in step (1) to obtain a steel ingot;
[0027] (3) When the taper of the steel ingot≤1.5%, carry out stress relief annealing to obtain a round tube; when the taper of the steel ingot>1.5%, carry out stress relief annealing, forging and annealing successively to obtain a round tube;
[0028] Wherein, in step (2), based on the total weight of the steel ingot as 100%, the chemical composition of the steel ingot is controlled as follows: C=0.07-0.14%, Si=0.17-0.37%, Mn=0.30-0.60%, Cr=0.90-1.20%, Ni=2.60-3.00%,...
Embodiment 1-3
[0048] (1) Carry out batching according to formula quantity, carry out electric arc furnace smelting, ladle furnace refining and vacuum degassing refining successively, obtain the electroslag consumable electrode that specification is Φ 300mm;
[0049] (2) the electroslag consumable electrode of step (1) gained Φ 300mm specification and the CaF that contains 65% by weight 2 , 20 wt% Al 2 o 3 , 7% by weight of CaO and 8% by weight of MgO in the quaternary electroslag system for electroslag remelting to obtain a steel ingot, the specification of the steel ingot is Φ550mm, and the taper of the steel ingot is 2%. Based on the total weight of the steel ingot as 100%, the chemical composition of the steel ingot is controlled as follows: C=0.07-0.14%, Si=0.17-0.37%, Mn=0.30-0.60%, Cr=0.90-1.20%, Ni= 2.60-3.00%, Mo=0.20-0.27%, V=0.04-0.10%, and the rest are unavoidable impurities and Fe.
[0050] (3) After the steel ingot obtained in step (2) is subjected to stress relief annealing...
Embodiment 4
[0052] Carry out according to the method described in embodiment 1-3, difference is, the taper of the steel ingot obtained in the step (2) is 1%, and in the step (3), the steel ingot only carries out stress relief annealing and obtains round tube billet.
PUM
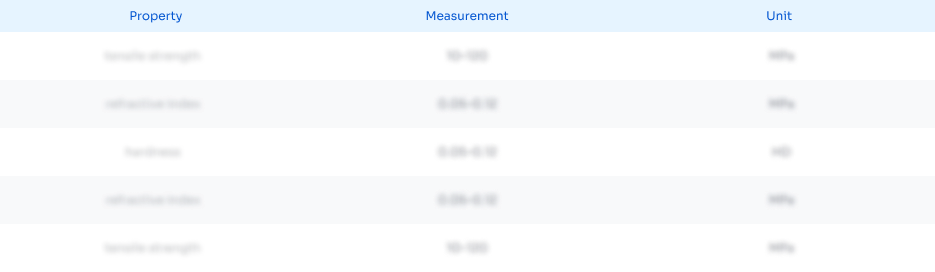
Abstract
Description
Claims
Application Information

- R&D
- Intellectual Property
- Life Sciences
- Materials
- Tech Scout
- Unparalleled Data Quality
- Higher Quality Content
- 60% Fewer Hallucinations
Browse by: Latest US Patents, China's latest patents, Technical Efficacy Thesaurus, Application Domain, Technology Topic, Popular Technical Reports.
© 2025 PatSnap. All rights reserved.Legal|Privacy policy|Modern Slavery Act Transparency Statement|Sitemap|About US| Contact US: help@patsnap.com