Silicon carbide-calcium hexaluminate-aluminum composite refractory material
A technology of calcium hexaaluminate and refractory materials, applied in the field of refractory materials, can solve the problems of destabilizing the matrix structure, low high-temperature mechanical strength, spalling, etc., so as to improve the high-temperature flexural strength, improve the high-temperature mechanical properties, and improve the composition and structure. Effect
- Summary
- Abstract
- Description
- Claims
- Application Information
AI Technical Summary
Problems solved by technology
Method used
Image
Examples
Embodiment 1
[0016] Weigh the particle size range from 10μm to 90μm, w (Al 2 o 3 +CaO)=99.0% dense calcium hexaaluminate powder 35kg; particle size range 10μm ~ 45μm, 5kg coated metal aluminum powder with sphericity 0.92, put them into a ball mill tank and mix them thoroughly for 1.5 hours by rolling ball mill; Weigh the particle size range from 0.1mm to 3mm, w (SiC) = 99.0% silicon carbide particles 60kg; put the silicon carbide particles into the roller sand mixer and stir for 5 minutes, add 4.5kg of phenolic resin and stir for 3 minutes, and mix the pre-mixed dense calcium hexaaluminate fine powder with the Put the coated metal aluminum powder into the roller sand mixer, stir together for 20 minutes, mix evenly and trap the material for 24 hours. Use a friction brick press to shape the fully trapped raw materials, and use an oven to dry the green body at 180°C for 24 hours. Put the baked green body into a corundum sagger, fill it with graphite powder, and heat it in a resistance fur...
Embodiment 2
[0018] Weigh the particle size range from 10μm to 45μm, w (Al 2 o 3 +CaO)=99.5% dense calcium hexaaluminate fine powder 30kg; particle size range 10μm ~ 45μm, coated metal aluminum powder 0.90 sphericity 7kg; Weigh the particle size range from 0.1mm to 3mm, w (SiC) = 98.5% silicon carbide particles 63kg. Put silicon carbide particles into the roller sand mixer and stir for 5 minutes, add 5kg of phenolic resin and stir for 3 minutes, put the pre-mixed dense calcium hexaaluminate fine powder and coated metal aluminum powder into the roller sand mixer In the middle, stir together for 20 minutes, after mixing evenly, the material will be trapped for 24 hours. Use a friction brick press to shape the fully trapped raw materials, and use an oven to dry the green body at 180°C for 24 hours. Put the baked green body into a corundum sagger, use graphite powder for landfill, and heat-treat in a resistance furnace at 1550°C for 5 hours to prepare a silicon carbide-calcium hexaalumina...
Embodiment 3
[0020] Weigh the particle size range from 10μm to 90μm, w (Al 2 o 3 +CaO)=98.5% dense calcium hexaaluminate fine powder 22kg; particle size range 10μm ~ 45μm, 8kg coated metal aluminum powder with a sphericity of 0.85, put them into a ball mill tank and mix them thoroughly for 1 hour by rolling ball mill; Weigh the particle size range from 0.1mm to 3mm, w (SiC) = 99.0% silicon carbide particles 70kg. Put silicon carbide particles into the roller sand mixer and stir for 5 minutes, add 4kg of amino water-based resin and stir for 3 minutes, put the pre-mixed dense calcium hexaaluminate fine powder and coated metal aluminum powder into the roller sand mixer In the machine, stir together for 30 minutes, and after mixing evenly, the material will be trapped for 12 hours. A friction brick press is used to shape the fully trapped raw materials, and an oven is used to dry the green body at 60°C and 110°C for 6 hours respectively. Put the baked green body into a corundum sagger, fi...
PUM
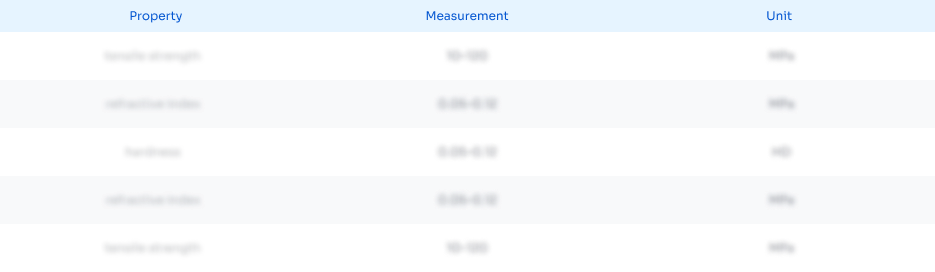
Abstract
Description
Claims
Application Information

- R&D Engineer
- R&D Manager
- IP Professional
- Industry Leading Data Capabilities
- Powerful AI technology
- Patent DNA Extraction
Browse by: Latest US Patents, China's latest patents, Technical Efficacy Thesaurus, Application Domain, Technology Topic, Popular Technical Reports.
© 2024 PatSnap. All rights reserved.Legal|Privacy policy|Modern Slavery Act Transparency Statement|Sitemap|About US| Contact US: help@patsnap.com