Method for preparing high-purity mullite material by taking molten silicon dioxide as silicon source
A technology of fused silica and silica, which is applied in the field of high-temperature ceramic materials, can solve the problems of high synthesis temperature of high-purity mullite, complex reaction methods, difficulty in meeting production requirements, etc., and achieve good high-temperature mechanical properties , high production efficiency, and the effect of improving high temperature toughness
- Summary
- Abstract
- Description
- Claims
- Application Information
AI Technical Summary
Problems solved by technology
Method used
Image
Examples
Embodiment 1
[0021] Step 1): Preparation of fused silica raw material;
[0022] Mix 90.5wt% natural quartz, 8.5wt% kaolinite and 1.0 wt% magnesia according to the mass percentage, and put them in a planetary ball mill (rotating speed 280r / min) for 3 hours, particle size ≤325 mesh, then mix The material is pressed into a green body under a pressure of 100 MPa, and the green body is dried and calcined at 1530° C. for 0.6 hours, and cooled to obtain a fused silica raw material.
[0023] Step 2): Use fused silica raw materials to prepare high-purity mullite materials;
[0024] Crush the fused silica raw material synthesized in step 1 and γ-Al 2 O 3 Fine powder press Al 2 O 3 / SiO 2 Ingredients with a molar ratio of 3:2. After the raw materials are co-milled (particle size ≤325 mesh), 4wt% of the above-mentioned raw material mass is added as a binder, molded at 120MPa, and calcined at 1600°C for 3 hours. Obtain high-purity mullite material.
[0025] The technical index of the high-purity mullite mater...
Embodiment 2
[0027] Step 1): Preparation of fused silica raw material;
[0028] According to the mass percentage, 94 wt% silica, 5.5 wt% γ-Al 2 O 3 Mix it with 0.5wt% yttrium oxide, put it into a planetary ball mill (rotating speed 280r / min), ball mill for 3 hours, particle size ≤325 mesh, then press the mixture into a green body under a pressure of 100MPa, and dry the green body at 100°C It is calcined at 1560°C for 0.5 hours and cooled to obtain a fused silica raw material.
[0029] Step 2): Use fused silica raw materials to prepare high-purity mullite materials;
[0030] Crush the fused silica raw material synthesized in step 1 and α-Al 2 O 3 Fine powder press Al 2 O 3 / SiO 2 Ingredients with a molar ratio of 3:2. After the raw materials are co-milled (particle size ≤325 mesh), 4wt% silica sol of the sum of the above raw materials is added as a binding agent, molded at 120MPa, and calcined at 1630°C for 4 hours. Pure mullite material.
[0031] The technical index of the high-purity mullite mat...
Embodiment 3
[0033] Step 1): Preparation of fused silica raw material;
[0034] Mix 86.6wt% of natural quartz, 12.8wt% of coal gangue and 0.6wt% of zinc oxide according to mass percentage, and then wet ball mill the mixture for 5 hours, with a particle size of ≤325 mesh, and press it into a blank under a pressure of 120MPa The green body is dried at 100°C and calcined at 1550°C for 0.6 hours. After cooling, the fused silica raw material is obtained.
[0035] Step 2): Use fused silica raw materials to prepare high-purity mullite materials;
[0036] Crush the fused silica raw material synthesized in step 1 and α-Al 2 O 3 Fine powder according to Al 2 O 3 / SiO 2 Ingredients with a molar ratio of 3:2. After the raw materials are co-milled (particle size ≤325 mesh), 4wt% of the above-mentioned raw material masses and 4wt% of the pulp waste liquid are added as a binding agent, molded at 120MPa, and calcined at 1630°C for 5 hours. High-purity mullite material.
[0037] The technical index of the high-pu...
PUM
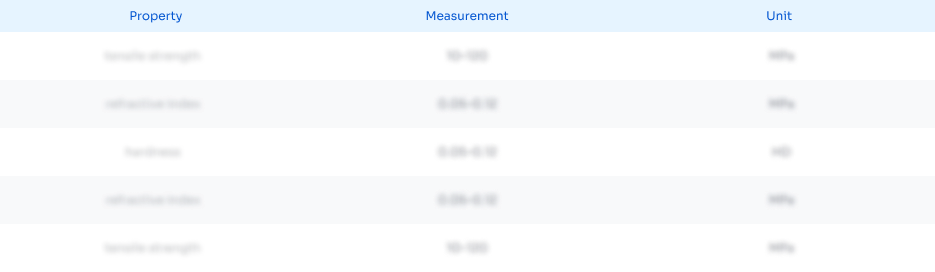
Abstract
Description
Claims
Application Information

- R&D Engineer
- R&D Manager
- IP Professional
- Industry Leading Data Capabilities
- Powerful AI technology
- Patent DNA Extraction
Browse by: Latest US Patents, China's latest patents, Technical Efficacy Thesaurus, Application Domain, Technology Topic, Popular Technical Reports.
© 2024 PatSnap. All rights reserved.Legal|Privacy policy|Modern Slavery Act Transparency Statement|Sitemap|About US| Contact US: help@patsnap.com