Production process of PTFE fiber cloth
A production process and fiber cloth technology, applied in the field of PTFE fiber cloth production technology, can solve the problems of reducing the service life of the fiber cloth, uneven concentration distribution, cracking of the fiber cloth, etc., and achieve the effect of improving the impregnation effect.
- Summary
- Abstract
- Description
- Claims
- Application Information
AI Technical Summary
Problems solved by technology
Method used
Image
Examples
Embodiment approach
[0044] As an embodiment of the present invention, the concentration of the mixed solution in the immersion device is 90mol / L; the temperature of the mixed solution in the immersion device is between 75-90°C;
[0045] The concentration of PTFE dispersion directly affects the surface finish, flatness, thickness and resin content of the product. When the concentration is too high, the thickness after each impregnation will be large, which will make the coating on the fiber cloth too thick and make the Cracks are produced on the surface of the fiber cloth, and the concentration of the mixed solution is 90mol / L when the present invention is dipped, so as to prevent the occurrence of an over-thick coating on the surface of the fiber cloth, thereby affecting the quality and quality of the fiber cloth, because the temperature of the mixed solution is between Between 75-90°C, so that the mixed solution can be better impregnated on the surface of the fiber cloth, so as to avoid the exces...
PUM
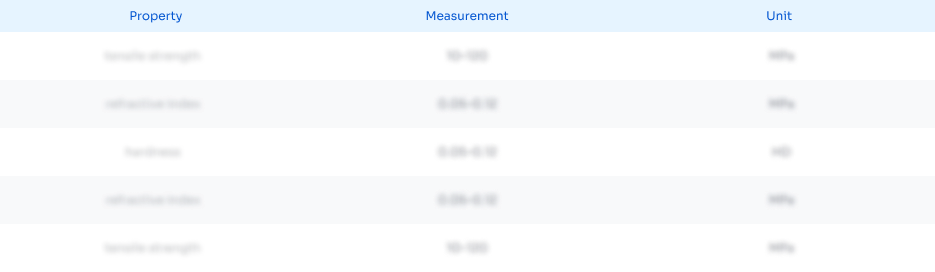
Abstract
Description
Claims
Application Information

- R&D
- Intellectual Property
- Life Sciences
- Materials
- Tech Scout
- Unparalleled Data Quality
- Higher Quality Content
- 60% Fewer Hallucinations
Browse by: Latest US Patents, China's latest patents, Technical Efficacy Thesaurus, Application Domain, Technology Topic, Popular Technical Reports.
© 2025 PatSnap. All rights reserved.Legal|Privacy policy|Modern Slavery Act Transparency Statement|Sitemap|About US| Contact US: help@patsnap.com