Separation method of raw material containing lead
A separation method and technology for raw materials, which are applied to the improvement of process efficiency, calcium/strontium/barium sulfate and other directions, can solve the problems of high separation cost of lead-containing raw materials, difficult separation of lead-zinc, and high cost of desulfurization of lead-containing raw materials
- Summary
- Abstract
- Description
- Claims
- Application Information
AI Technical Summary
Problems solved by technology
Method used
Image
Examples
Embodiment 1
[0097] (1) Add 10kg of zinc oxide ore (containing 7.5% zinc, 1.1% lead, 10.4% calcium, and 1.5% magnesium) to a 50L reaction kettle, add water to 50L, and use sulfuric acid to adjust the pH value at 1.0- 1.2, reaction temperature 50°C, react for 5 hours, filter to obtain 45L of zinc-containing solution and 11.5kg of filter residue;
[0098] (2) Adjust the pH value of the filtrate obtained in step (1) to 3.0 with sodium hydroxide, react at 100° C. for 5 hours, and filter to obtain iron oxide slag and filtrate;
[0099] (3) adding 50g of zinc powder to the filtrate gained in step (2), reacting for 4h, filtering to obtain purified slag and filtrate;
[0100] (4) Add 100ml of 30% hydrogen peroxide and 700g of ammonium carbonate to the filtrate obtained in step (3), react at 60°C for 3h, filter to obtain filtrate and purified residue;
[0101] (5) Add the filtrate obtained in step (4) into another reaction kettle, heat and evaporate to 25L, cool to 20°C, and filter to obtain ammon...
Embodiment 2
[0113] (1) Add 100g of scrap lead-acid battery lead paste (70.5% lead) into a 1L reactor, add 50g of sodium sulfate, 35g of cobalt chloride, 15g of nickel nitrate, 25g of nitrilotriacetic acid, and 100g of hydroxyethylethylenediamine Triacetic acid, 25g of ethylenediamine, 100g of diethylenetriamine, add water to make up to 1L, use sodium hydroxide to adjust the pH value between 9.9-10.5, and add 30g of calcium oxide, the reaction temperature is 60°C, react for 5h, filter, Obtain 1L of lead-containing solution and 70g of filter residue;
[0114] (2) Add 5 g of sodium carbonate to the lead-containing solution obtained in step (1), react for 1 h at 70° C., filter to obtain filtrate and purification residue;
[0115] (3) In the solution obtained in step (2), feed carbon dioxide at a speed of 290ml / L, use sodium hydroxide to adjust the pH value of the solution between 7.0-7.5, the reaction temperature is 50°C, and the reaction time is 4h. , separate, wash, dry, obtain 98g lead ca...
Embodiment 3
[0119] (1) Mix 50kg of blast furnace ash (containing 9.1% zinc, 2.3% lead, 40.5% iron, and 2.7% calcium) with 20kg ammonium sulfate, heat treatment at 200°C for 5 hours, then heat up to 500°C, and continue heat treatment for 5 hours , the gas generated during heat treatment is absorbed into lye with water and then cooled;
[0120](2) Add the treated blast furnace ash obtained in step (1) into a 100L reaction kettle, add 1kg of sodium sulfate, adjust the volume to 100L with water, use sulfuric acid to adjust the pH value between 0.8-1.0, and react at a temperature of 90°C. 5h, filter, and wash the filter cake with 20L of water to obtain 100L of zinc-containing solution and 41kg of filter residue;
[0121] (3) adjusting the pH value of the filtrate obtained in step (2) to above 4.0 with lye, reacting at 95° C. for 4 hours, and filtering to obtain the jarosite slag and filtrate;
[0122] (4) adding 1kg of zinc powder to the filtrate gained in step (3), reacting for 4h, filtering...
PUM
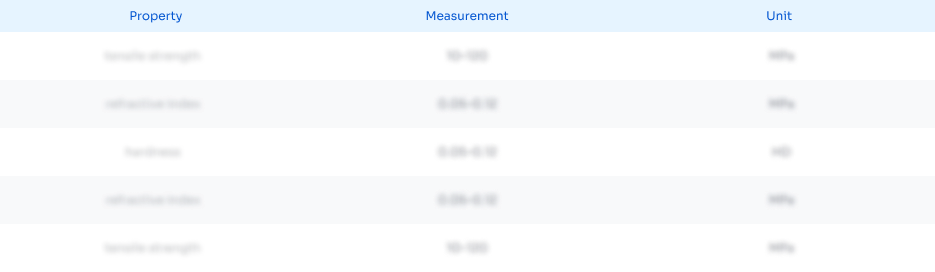
Abstract
Description
Claims
Application Information

- Generate Ideas
- Intellectual Property
- Life Sciences
- Materials
- Tech Scout
- Unparalleled Data Quality
- Higher Quality Content
- 60% Fewer Hallucinations
Browse by: Latest US Patents, China's latest patents, Technical Efficacy Thesaurus, Application Domain, Technology Topic, Popular Technical Reports.
© 2025 PatSnap. All rights reserved.Legal|Privacy policy|Modern Slavery Act Transparency Statement|Sitemap|About US| Contact US: help@patsnap.com