Distributed multi-physical-field coupling control system for simulating sweating and cooling
A coupled control, sweat cooling technology, applied in electrical digital data processing, CAD numerical modeling, instruments, etc., can solve the problems of complex network topology, mutual influence and restriction of computing function and communication, etc., to avoid process deadlock and save energy. To repeatedly start the program, improve the effect of efficiency
- Summary
- Abstract
- Description
- Claims
- Application Information
AI Technical Summary
Problems solved by technology
Method used
Image
Examples
Embodiment Construction
[0056] The present invention will be further elaborated below in conjunction with embodiment.
[0057] Such as figure 1 Shown is a schematic diagram of sweat cooling. The spherical part in the figure is the sweating end of the porous medium. The external main flow flows from left to right, and the coolant seeps out from the porous medium and mixes with the main flow. To simulate this problem, the flow outside the head and the pore flow in the porous media need to be simulated. The external mainstream flow is simulated by the mainstream calculation module, the pore flow in the porous medium is simulated by the porous medium calculation module, and the seepage interface is coupled through the method of the invention.
[0058] figure 2 The topological schematic diagram of the flow process simulated by this method includes a coupling control module, a mainstream calculation module, and a porous medium calculation module.
[0059] image 3 It is a flowchart of a method for cou...
PUM
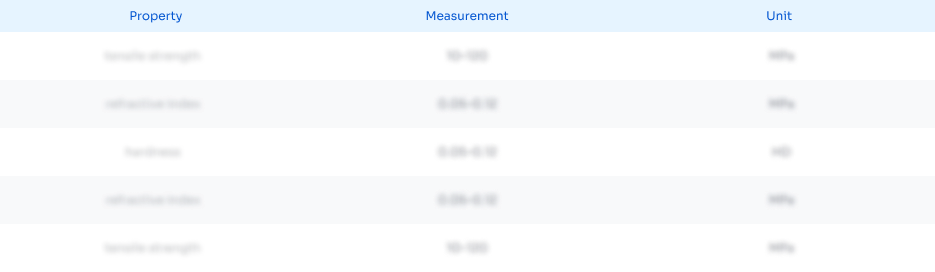
Abstract
Description
Claims
Application Information

- Generate Ideas
- Intellectual Property
- Life Sciences
- Materials
- Tech Scout
- Unparalleled Data Quality
- Higher Quality Content
- 60% Fewer Hallucinations
Browse by: Latest US Patents, China's latest patents, Technical Efficacy Thesaurus, Application Domain, Technology Topic, Popular Technical Reports.
© 2025 PatSnap. All rights reserved.Legal|Privacy policy|Modern Slavery Act Transparency Statement|Sitemap|About US| Contact US: help@patsnap.com