Method for milling and repairing composite material by high-pressure abrasive particle water jet
A composite material and water jet technology, which is applied in the field of material processing, can solve the problems of unfavorable prepreg filling and curing repair, high heat, poor surface roughness, etc., to achieve close bonding, low roughness Ra, and repair The effect of the process
- Summary
- Abstract
- Description
- Claims
- Application Information
AI Technical Summary
Problems solved by technology
Method used
Image
Examples
Embodiment Construction
[0020] The implementation of high-pressure abrasive water jet repair composite material technology, the specific steps include:
[0021] (1) Clamping: Fix and clamp the part to ensure that the part fits with the positioning surface of the fixture. Select a position with good rigidity, easy support, and no interference with the water jet to press it through the pressure plate. Rubber pads need to be added at the pressed place to avoid Crushing the part substrate.
[0022] (2) Alignment: Alignment The surface jump of the plane to be processed is not greater than 0.10mm. This step can be carried out simultaneously with step (1).
[0023] (3) Tool setting: tool setting confirms the origin of the program and the starting point of the cutting tool;
[0024] (4) Parameter setting: According to the actual processing needs, set the feed F in the range of 2m / min to 6m / min, the pressure P in the range of 400bar to 1000bar, and the overlapping amount S in the range of 0.75mm to 1.5mm; T...
PUM
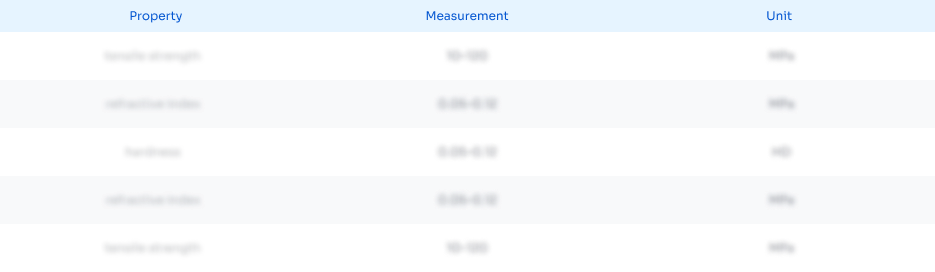
Abstract
Description
Claims
Application Information

- R&D Engineer
- R&D Manager
- IP Professional
- Industry Leading Data Capabilities
- Powerful AI technology
- Patent DNA Extraction
Browse by: Latest US Patents, China's latest patents, Technical Efficacy Thesaurus, Application Domain, Technology Topic, Popular Technical Reports.
© 2024 PatSnap. All rights reserved.Legal|Privacy policy|Modern Slavery Act Transparency Statement|Sitemap|About US| Contact US: help@patsnap.com