AlCrYN/AlCrSiN nano composite gradient coating on surface of pressure casting die and preparation method thereof
A die-casting mold and nano-composite technology, applied in coating, metal material coating process, ion implantation plating, etc., can solve the problems of insufficient research on anti-adhesion performance, achieve good temperature resistance and anti-adhesion effect, reduce production cost, Effect of good anti-adhesion and temperature resistance properties
- Summary
- Abstract
- Description
- Claims
- Application Information
AI Technical Summary
Problems solved by technology
Method used
Image
Examples
Embodiment 1
[0042] Prepare the die-casting mold, and sandblast the surface of the die-casting mold under the condition of sandblasting pressure of 0.3MPa, so that the surface roughness is R Z 1.6. The surface roughness of the die-casting mold prepared in this step is suitable, which is beneficial to the deposition of the coating and improves the adhesion of the coating.
[0043] Place the die-casting mold into the arc ion plating equipment for the next step.
[0044] Specifically, such as figure 1 As shown, the vacuum chamber of the arc ion plating equipment is surrounded by the furnace wall, and the size of the vacuum chamber is Φ1000x1000mm. The vacuum chamber is provided with an etching source 1 and an exhaust system 5 . Six columns of targets are installed on the wall of the vacuum furnace, namely the first CrY target 2, the second CrY target 3, the first AlCrY target 4, the first AlCrY target 7, the first AlCrSi target 8, and the second AlCrSi target 9. Further, a rotatable workp...
Embodiment 2
[0065] In this example, on the basis of Example 1, the process parameters of the preparation are adjusted. Only the differences are described here, and the similarities are not repeated here.
[0066] Prepare the die-casting mold, and perform sandblasting on the die-casting mold under the condition of sandblasting pressure of 0.8MPa, so that the surface roughness is Rz50.
[0067] Subsequently, the die-casting mold was nitrided under the condition of 500Pa, and the nitriding depth was 200 microns; and the die-casting mold was ion-etched under the condition of 500°C, the etching voltage was 150V, and the etching depth was 0.5 micron.
[0068] After ion etching, the AlCrYN / AlCrSiN nanocomposite gradient coating on the surface of the die-casting mold was prepared by arc ion plating equipment. First, the CrY target is turned on, and a 50nm CrY binding layer is deposited under the conditions of 0.5Pa and 150V.
[0069] Nitrogen gas was introduced, and a 500nm CrYN transition laye...
Embodiment 3
[0074] In this example, on the basis of Example 1, the process parameters of the preparation are adjusted. Only the differences are described here, and the similarities are not repeated here.
[0075] Prepare the die-casting mold, and blast the surface of the die-casting mold under the condition of sandblasting pressure of 0.5MPa to make the surface roughness R Z 10.
[0076]Subsequently, the die-casting mold was nitrided under the condition of 400Pa, and the nitriding depth was 100 microns; at 400°C, the mold was ion-etched, the etching voltage was 100V, and the etching depth was 0.3 microns.
[0077] After ion etching, the AlCrYN / AlCrSiN nanocomposite gradient coating on the surface of the die-casting mold was prepared by arc ion plating equipment. First, the CrY target is turned on, and a 40 nm thick CrY binding layer is deposited under the conditions of 0.2 Pa and 100 V.
[0078] Nitrogen gas was introduced, and a CrYN transition layer with a thickness of 200 nm was dep...
PUM
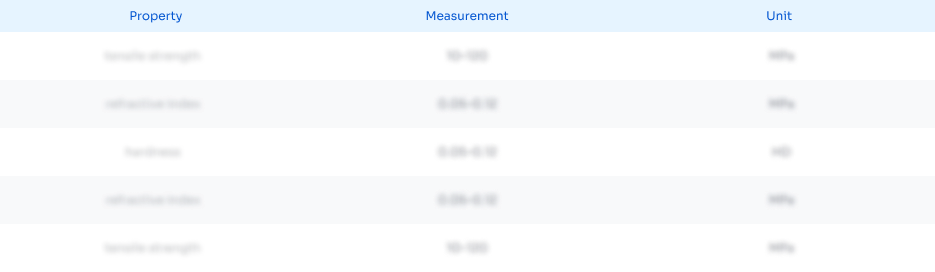
Abstract
Description
Claims
Application Information

- Generate Ideas
- Intellectual Property
- Life Sciences
- Materials
- Tech Scout
- Unparalleled Data Quality
- Higher Quality Content
- 60% Fewer Hallucinations
Browse by: Latest US Patents, China's latest patents, Technical Efficacy Thesaurus, Application Domain, Technology Topic, Popular Technical Reports.
© 2025 PatSnap. All rights reserved.Legal|Privacy policy|Modern Slavery Act Transparency Statement|Sitemap|About US| Contact US: help@patsnap.com