Method for preparing organic calcium molding material from alkali reduction waste water
A technology of alkali reduction wastewater and molding materials, which is applied in the field of water treatment, can solve the problems of unused water temperature for reduction, waste of acid and alkali resources, energy loss, etc., to improve mechanical properties, reduce biochemical treatment load, and improve processing The effect of the process
- Summary
- Abstract
- Description
- Claims
- Application Information
AI Technical Summary
Problems solved by technology
Method used
Examples
Embodiment 1
[0023] A method for preparing organic calcium molding materials from alkali-reduction waste water of the present invention comprises the following steps:
[0024] (1) After the hot alkali weight loss water from the upstream process passes through the activated carbon filter, it is stored in the storage tank for heat preservation;
[0025] (2) With continuous stirring, add stearic acid into the liquid of (1) under heat preservation until it is completely dissolved, and the pH at the end point is controlled to be 7;
[0026] (3) With continuous stirring, add the pre-configured calcium hydroxide slurry into the solution obtained in step (2), continue stirring and reacting for 20 minutes in a homogenizer with a rotating speed of 2500r / min, centrifuge and dry, that is obtain the target product.
[0027] Further, the mass concentration of sodium terephthalate in the alkali reduction water is 2%.
[0028] Further, the holding temperature of the alkali-reduced water in step (2) is 6...
Embodiment 2
[0033] The difference between embodiment 2 and embodiment 1 is:
[0034] In step (2), the pH of the control end point is 8;
[0035] In step (3), under continuous stirring, add the pre-configured calcium hydroxide slurry into the solution obtained in step (2), continue to stir and react for 40 minutes in a homogenizer with a rotating speed of 1000r / min, centrifuge, After drying, the target product is obtained.
[0036] Further, the mass concentration of sodium terephthalate in the alkali reduction water is 5%.
[0037] Further, the holding temperature of the alkali-reduced water in step (2) is 65°C.
[0038] Further, the mass percent concentration of the calcium hydroxide slurry is 15%.
[0039] Further, the reaction molar ratio of calcium hydroxide to organic acid sodium salt is 1.1:1.
[0040] Furthermore, the activity of lime is 360ml / 4N-HCl.
Embodiment 3
[0042] The difference between embodiment 3 and embodiment 1 is:
[0043] In step (2), the pH of the control end point is 7.5;
[0044] In step (3), under continuous stirring, add the pre-configured calcium hydroxide slurry into the solution obtained in step (2), continue to stir and react for 30 minutes in a homogenizer with a rotating speed of 2000r / min, centrifuge, After drying, the target product is obtained.
[0045] Further, the mass concentration of sodium terephthalate in the alkali reduction water is 3.5%.
[0046] Further, the holding temperature of the alkali-reduced water in step (2) is 70°C.
[0047] Further, the mass percent concentration of the calcium hydroxide slurry is 12%.
[0048] Further, the reaction molar ratio of calcium hydroxide and organic acid sodium salt is 1:1.
[0049] Furthermore, the activity of lime is 400ml / 4N-HCl.
PUM
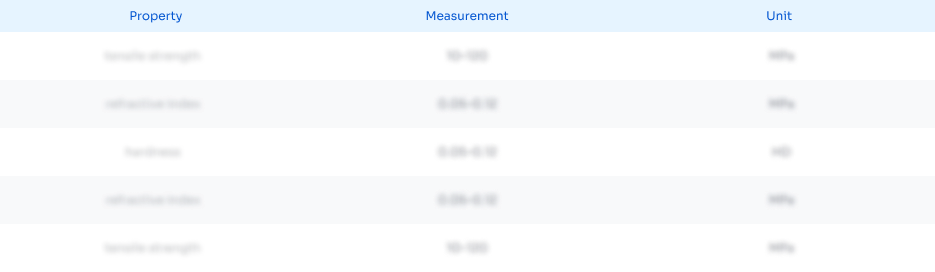
Abstract
Description
Claims
Application Information

- R&D Engineer
- R&D Manager
- IP Professional
- Industry Leading Data Capabilities
- Powerful AI technology
- Patent DNA Extraction
Browse by: Latest US Patents, China's latest patents, Technical Efficacy Thesaurus, Application Domain, Technology Topic, Popular Technical Reports.
© 2024 PatSnap. All rights reserved.Legal|Privacy policy|Modern Slavery Act Transparency Statement|Sitemap|About US| Contact US: help@patsnap.com