Preparation method of foam base material special for cultivation and cultivation method
A technology of substrate materials and biomass raw materials, applied in the field of plant cultivation, can solve the problems of being unable to meet the requirements of cultivation substrate materials, unable to replace the advantages of traditional peat resources, and using methods that cannot get rid of the cultivation mode, so as to achieve good water absorption and water retention performance and applicability Expansive, lightweight and high-strength effects
- Summary
- Abstract
- Description
- Claims
- Application Information
AI Technical Summary
Problems solved by technology
Method used
Image
Examples
Embodiment 1
[0045] A method for preparing a special foaming matrix material for cultivation, comprising the following steps:
[0046] 1) Preparation of biomass liquefaction product resin
[0047] ① Prepare the following raw materials in parts by weight: 100 parts of biomass raw materials (bamboo), 30 parts of composite liquefaction agent (2:1 phenol and polyethylene glycol-400), 20 parts of liquefaction catalyst (sulfuric acid), alkaline catalyst ( 40% caustic soda solution) 20 parts, formaldehyde (38% industrial formaldehyde solution) 60 parts;
[0048] ②Raise the temperature of the reactor to 60°C, add the composite liquefaction agent and stir evenly, add the biomass raw material and stir, add the catalyst for liquefaction and stir at a constant speed, heat up to 120°C, keep it warm for 10 minutes, stop the reaction and cool down to 60°C, Add a basic catalyst to adjust the pH value to alkaline, add formaldehyde, raise the temperature to 85°C, keep it warm for 20 minutes, stop the react...
Embodiment 2
[0053] A method for preparing a special foaming matrix material for cultivation, comprising the following steps:
[0054] 1) Preparation of biomass liquefaction product resin
[0055] ① Prepare the following raw materials in parts by weight: 100 parts of biomass raw materials (wood), 90 parts of composite liquefaction agent (3:1 phenol and polyethylene glycol-400), 25 parts of liquefaction catalyst (hydrochloric acid), alkaline catalyst ( 40% soda ash solution) 30 parts, formaldehyde (40% industrial formaldehyde solution) 80 parts;
[0056] ②Raise the temperature of the reactor to 60°C, add the composite liquefaction agent and stir evenly, add the biomass raw material and stir, add the catalyst for liquefaction and stir at a constant speed, heat up to 125°C, keep it warm for 20 minutes, stop the reaction and cool down to 60°C, Add a basic catalyst to adjust the pH value to alkaline, add formaldehyde, raise the temperature to 90°C, keep it warm for 25 minutes, stop the reactio...
Embodiment 3
[0061] A method for preparing a special foaming matrix material for cultivation, comprising the following steps:
[0062] 1) Preparation of biomass liquefaction product resin
[0063] ① Prepare the following raw materials in parts by weight: 100 parts of biomass raw materials (crop straw), 60 parts of composite liquefaction agent (1:1 phenol and polyethylene glycol-400), 15 parts of catalyst for liquefaction (nitric acid), alkaline catalyst (50% caustic soda solution) 40 parts, formaldehyde (40% industrial formaldehyde solution) 40 parts;
[0064] ②Raise the temperature of the reactor to 60°C, add the composite liquefaction agent and stir evenly, add the biomass raw material and stir, add the liquefaction catalyst and stir at a constant speed, heat up to 130°C, keep it warm for 30 minutes, stop the reaction and cool down to 60°C, Add a basic catalyst to adjust the pH value to alkaline, add formaldehyde, raise the temperature to 95°C, keep it warm for 30 minutes, stop the reac...
PUM
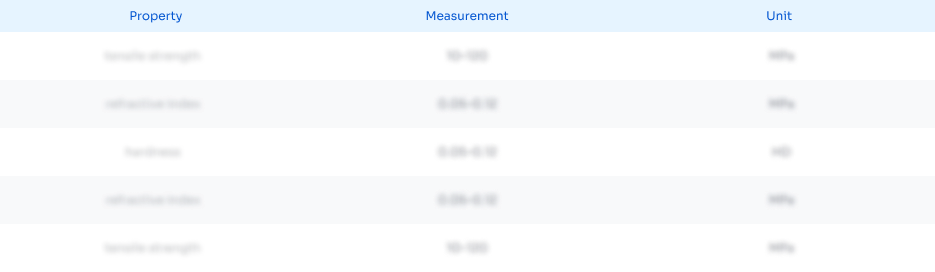
Abstract
Description
Claims
Application Information

- Generate Ideas
- Intellectual Property
- Life Sciences
- Materials
- Tech Scout
- Unparalleled Data Quality
- Higher Quality Content
- 60% Fewer Hallucinations
Browse by: Latest US Patents, China's latest patents, Technical Efficacy Thesaurus, Application Domain, Technology Topic, Popular Technical Reports.
© 2025 PatSnap. All rights reserved.Legal|Privacy policy|Modern Slavery Act Transparency Statement|Sitemap|About US| Contact US: help@patsnap.com